In this era of climate emergency, we are beginning to look beyond sustainability to regenerative design – but what does this really mean and how do we define regenerative textiles and materials?
With human activities already causing major harm to the planet, current efforts around sustainability don’t go far enough to tackle the environmental crisis we are facing. Regenerative design is committed to putting back better – creating holistic creative practices that restore or renew resources, leave a positive environmental impact and help communities thrive.
Future design consultancy FranklinTill curated a global showcase of cutting-edge textiles and materials to illustrate the principles of regenerative design. By celebrating pioneering designers, producers and manufacturers at the forefront of regenerative design, we can facilitate and accelerate change, enabling both people and the planet to flourish.
Enriching Communities
How can we enrich the lives of the people producing our materials and products?
In order to go beyond sustainability and become regenerative, we must focus on the social as well as environmental impact of production. Enriching Communities spotlights how materials are being made and by whom, looking to improve livelihoods with better pay, working conditions and future prospects.
Fernando Laposse
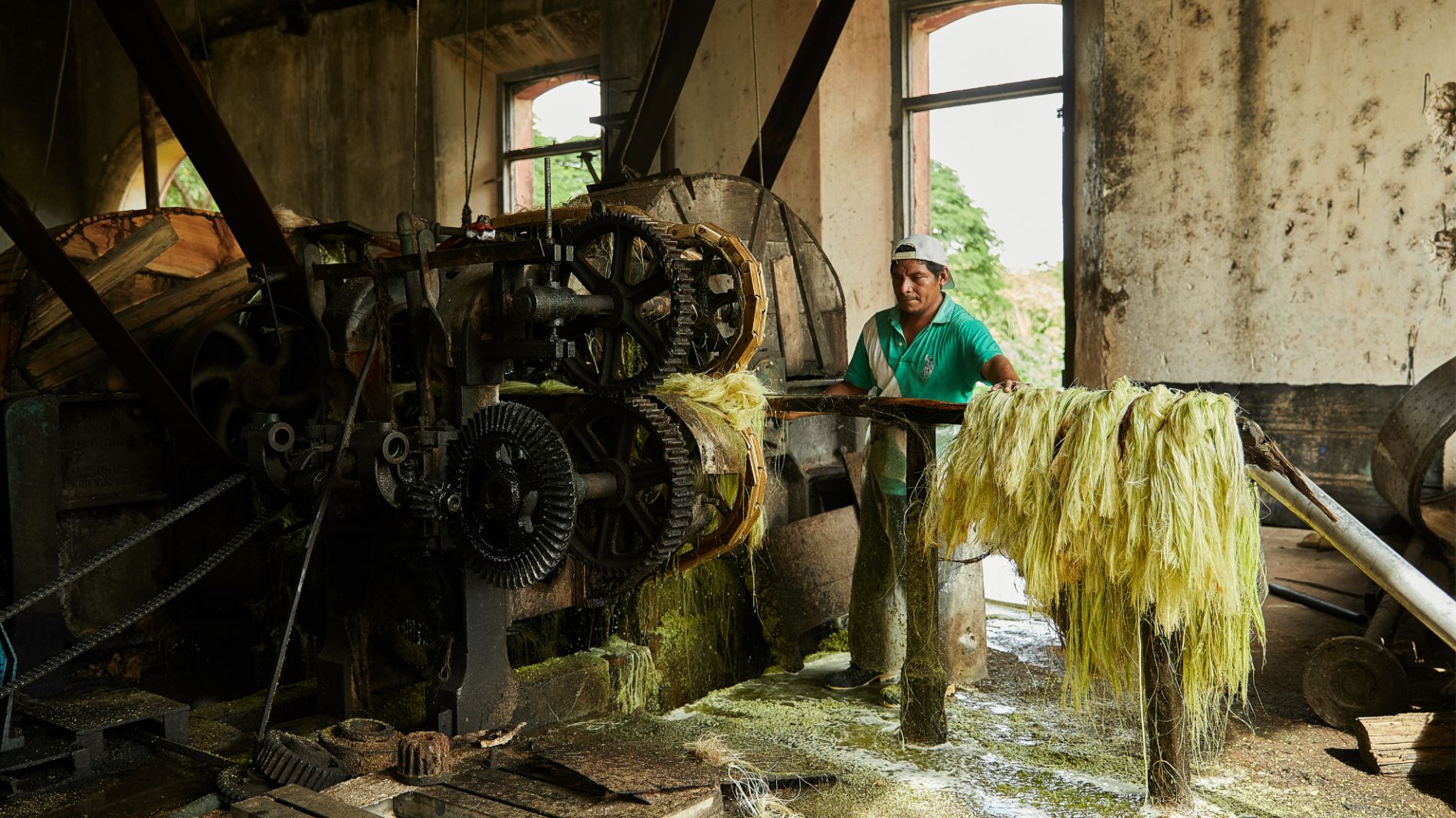
Product designer Fernando Laposse collaborates with local communities in his home country of Mexico, transforming natural materials into beautiful design objects. Regenerating traditional agricultural practices, his projects provide fair pay and empower vulnerable communities.
Ongoing work with the agave plant - a cactus used to make tequila - is reviving a local community’s land destroyed by modern farming. Sisal - derived from agave leaves - is a strong fibrous material widely used before the onset of plastic, which Laposse now uses in a range of striking ‘hairy’ furniture. Growing agave in a network of trenches allows farmers to capture water and repopulate fields, while the wider community produces Laposse’s sisal pieces. Generating regular income, this project illustrates how the power of design can regenerate environmental and social ecosystems.
fernandolaposse.com
@fernandolaposse
The Anou Cooperative
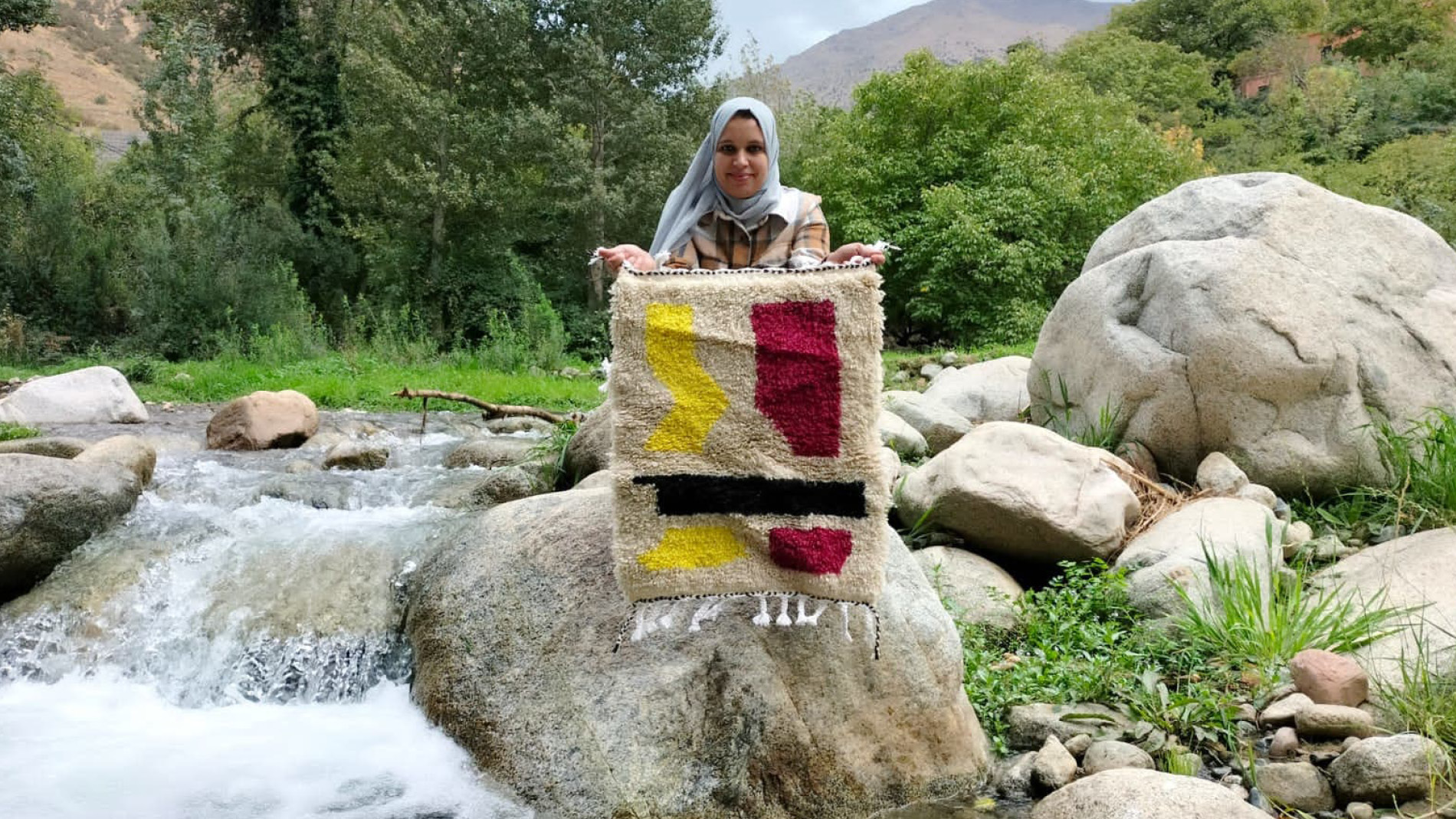
The Anou Cooperative is an artisan owned and managed collective of over 600 crafts people, workshops and associations across Morocco. Its aim is to build regenerative material supply chains, move beyond fair trade, cut out the middleman and empower the Moroccan craft economy.
Members gain access to affordable, quality, non-toxic materials and dyes that improve working conditions and local environments, as well as training, skills and support to grow their businesses online. Anou’s technology allows artisans to photograph and post their products in an online marketplace and communicate directly with clients. Artisans earn 80% of each purchase price, with the remaining 20% invested back into the Anou community to empower the collective for the future.
Fine Cell Work
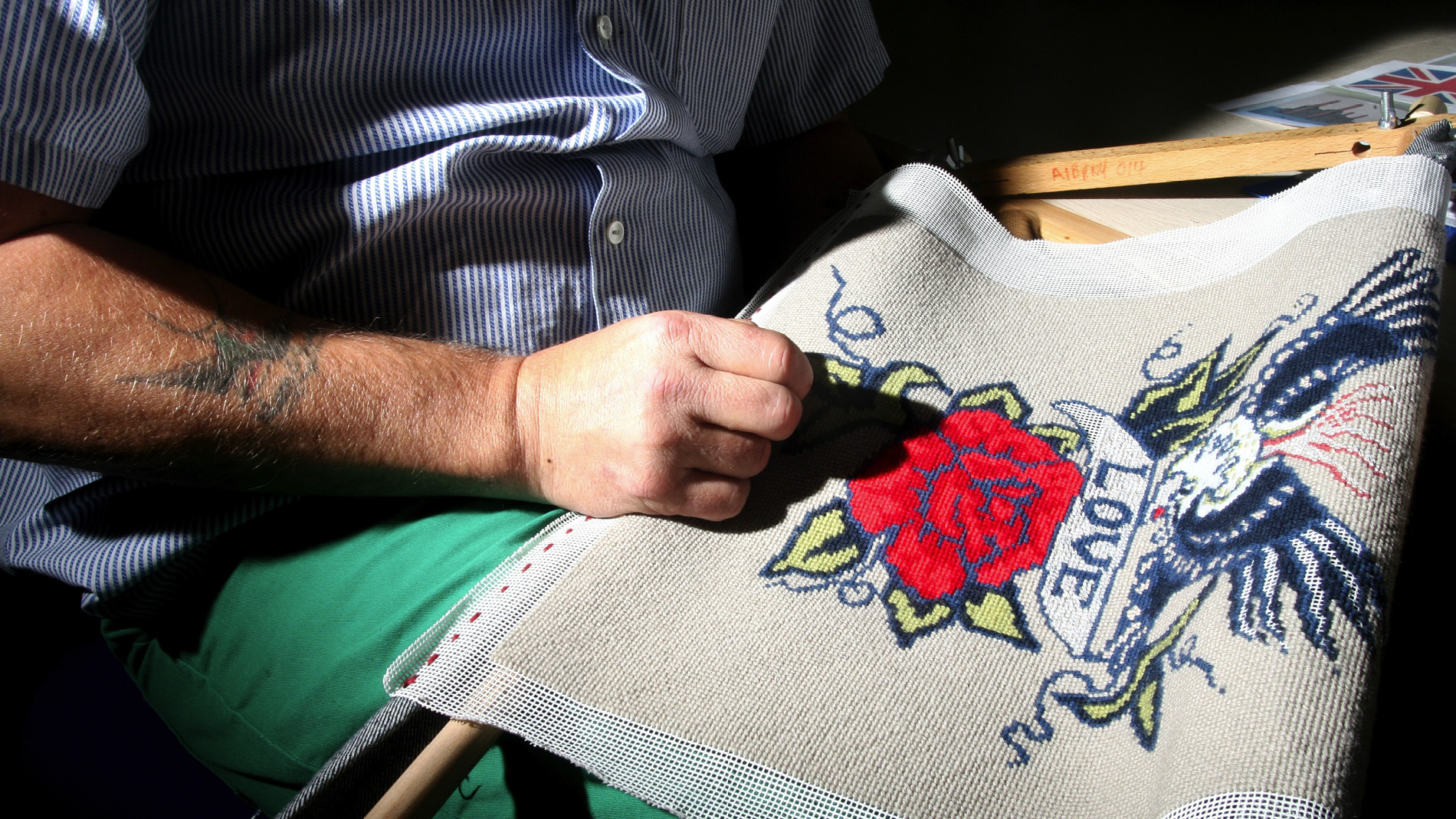
UK charity and social initiative Fine Cell Work teaches needlework skills in prisons. Providing prisoners with a purpose-led activity and paying them for their work provides emotional support and future employment opportunities.
Helping prisoners and prison leavers rebuild their lives and avoid returning to crime, Fine Cell Work’s volunteers run stitching groups in prisons and with apprentices in a post-release training programme. Collaborating with well-known designers on a range of homeware and fashion accessories, sewing kits are sent to prisoners to complete in their cells, the only paid work that can be carried out in UK prisons. These hand-crafted pieces are transformed into finished products in prison workshops, then sold in an online shop and at events.
Replenishing the Land
How can we grow and harvest materials in a way that has a positive impact on the land?
Focused on high yields with an over-reliance on pesticides and water, modern industrial farming has had a damaging effect on the land. Regenerative farming works holistically to reverse this, rebuilding organic soil matter and sequestering carbon in soil, wetlands and trees, as well as retaining water and reducing the use of artificial pesticides and fertilisers.
BioPuff® by Ponda
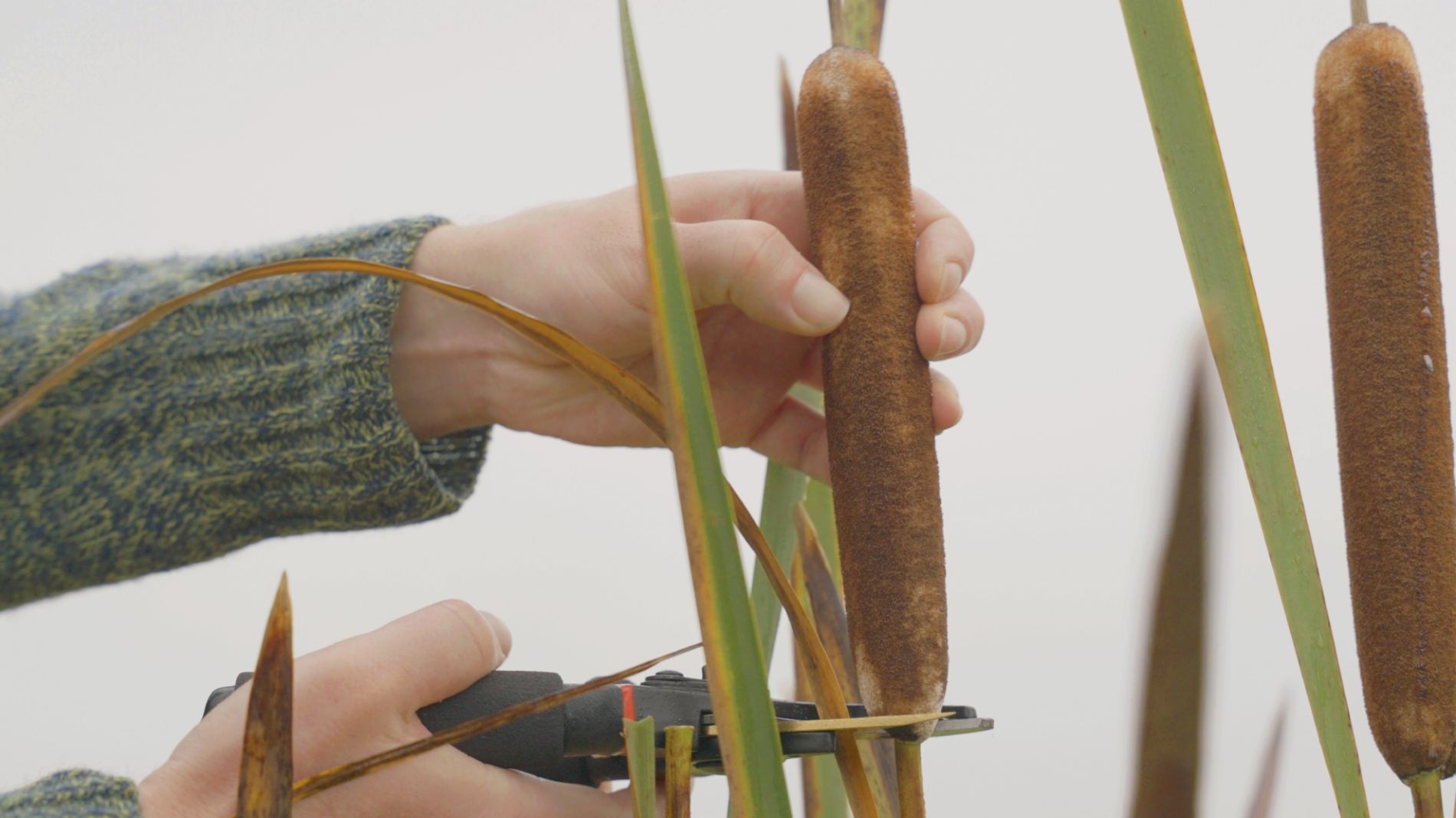
UK materials science company Ponda makes planet-positive textiles from plant-based raw materials. Restoring damaged ecosystems through regenerative agriculture, they are creating future-thinking supply chains.
Sourcing materials through farming projects in England, Scotland and Germany, Ponda designs restorative farming practices to benefit each local environment’s needs. Methods include the removal of invasive crops, and re-wetting dried-out peatlands to restore ecosystems and nurture carbon levels. BioPuff® is a fibre filler material with insulating properties made from bulrush plants grown on wetlands. Created with low-energy, waterless processes, this high-performance product naturally biodegrades in compostable conditions, safely re-entering the environment with a traceable life span.
Sebastian Cox
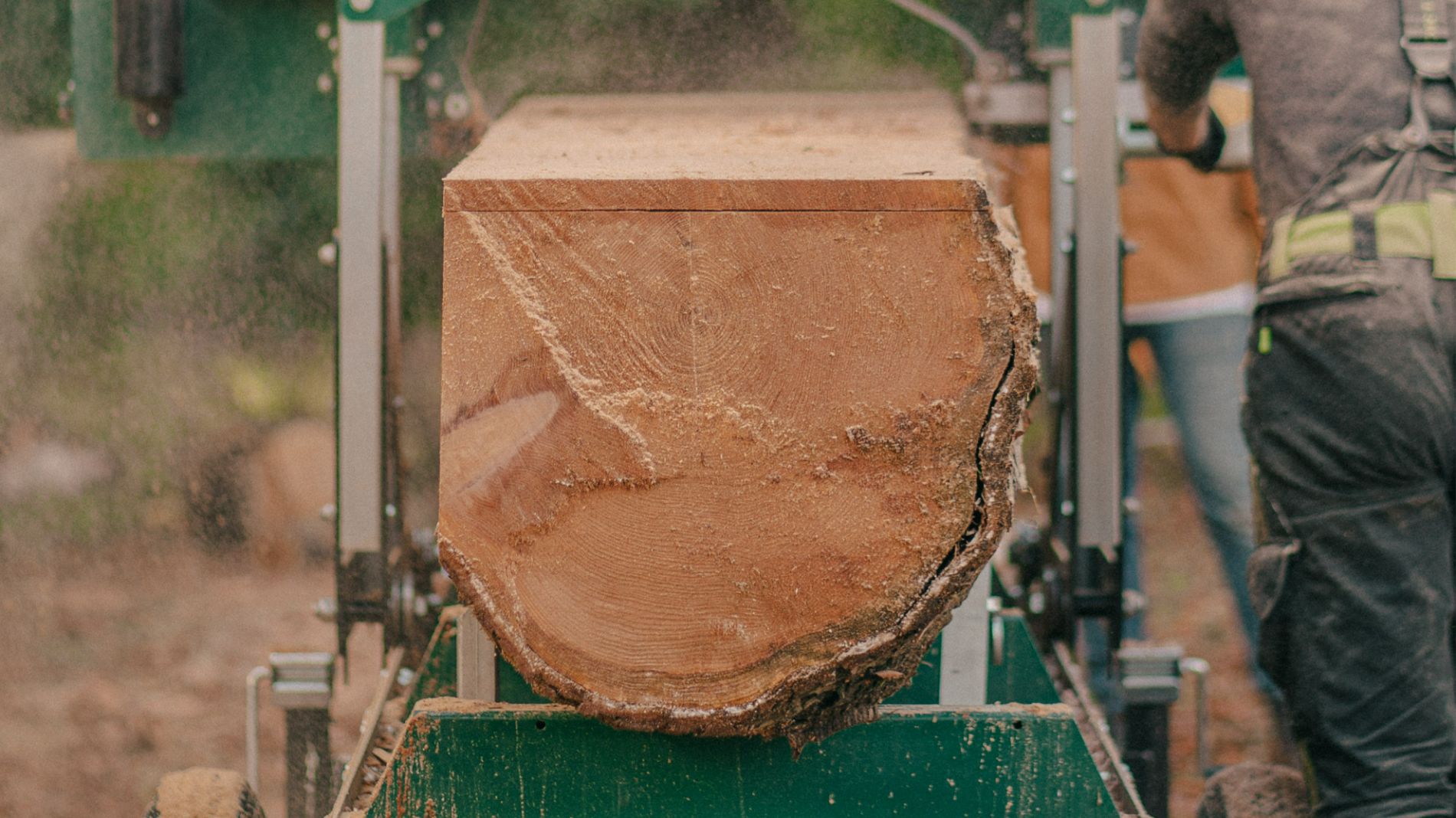
Fine furniture maker Sebastian Cox’s “nature-first perspective” guides his design process, sourcing materials from an ancient woodland in Kent, UK, also managed by his company.
Sebastian Cox coppices trees to encourage natural regrowth and creates rewilding projects that allow habitats to slowly return to their natural state. These processes offer access to a wider range of British wood species and foraged resources such as leather and mycelium, and showcase Cox’s belief that the design industry should value material localisation and availability above aesthetics. Harvesting, milling and kilning timber in-house before crafting it in a zero-waste, carbon-counting workshop in South London, Cox’s pieces are designed to last, and celebrate the non-standardisation of nature.
Good Earth Cotton
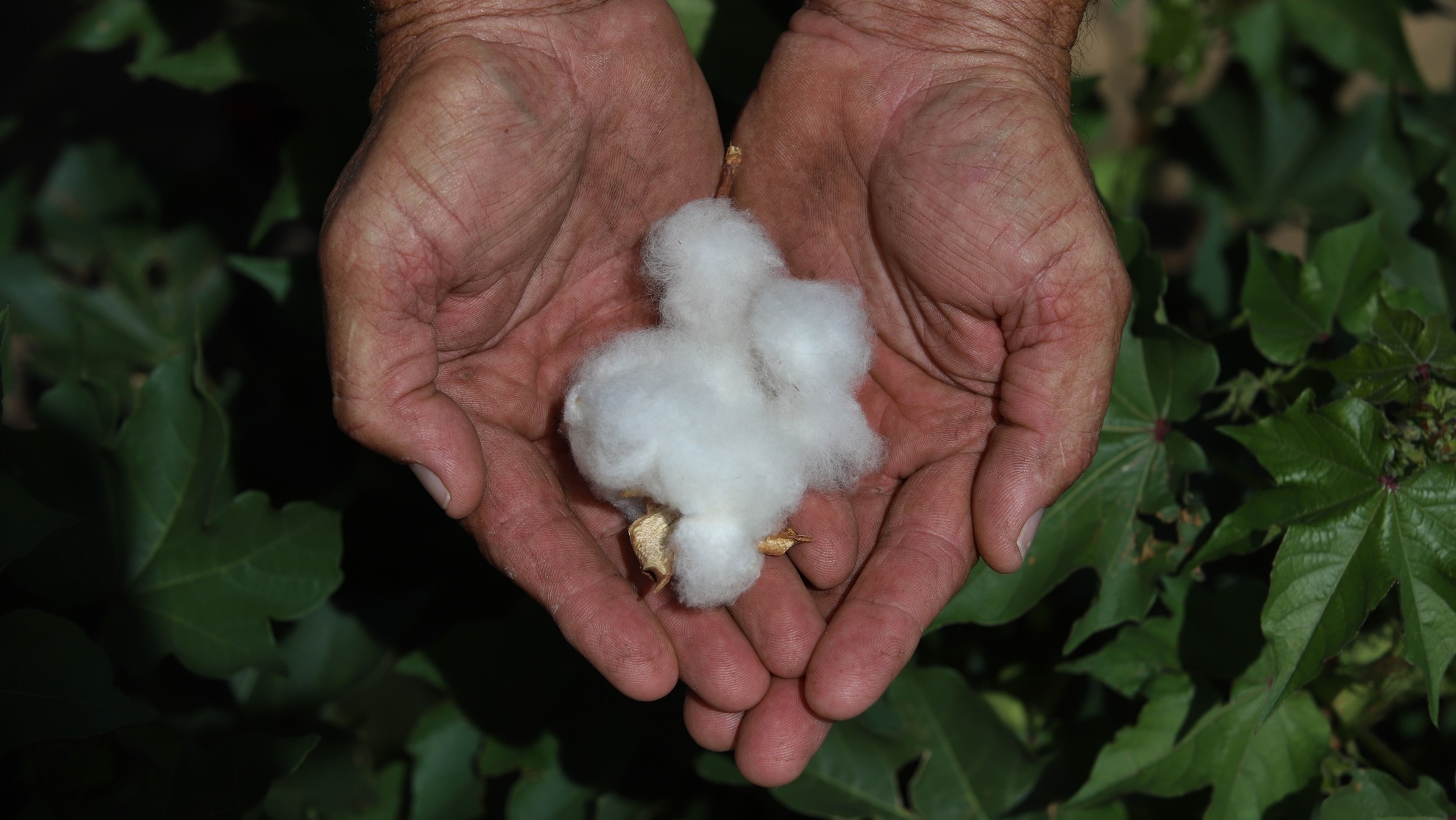
Good Earth Cotton is an Australian-based regenerative farming programme that helps global producers and communities create climate positive, fully traceable cotton supply chains.
Providing a high yield, environmentally-beneficial alternative to conventional cotton agriculture, Good Earth Cotton’s process focuses on enriching living soil through minimal disturbance and preserving moisture. Healthy plants capture and store carbon from the atmosphere, nourishing the soil through their roots and growing via photosynthesis, with seasonal crop rotation providing ground cover and interrupting pest and disease cycles. Participating cotton growers are measured and audited each harvest. The FibreTrace® transparency technology is embedded into the raw fibres to provide blockchain authentication throughout its life cycle.
Preserving Heritage
How can we utilise knowledge from ancient material and textile production, and ensure these skills continue to thrive?
Many indigenous practices are regenerative by nature, working in harmony with the land and local communities. By acknowledging and celebrating the value of cultural heritage and craftsmanship and learning from its ecological wisdom, we can protect valuable skills and knowledge from being lost to technology and globalisation.
Irthi
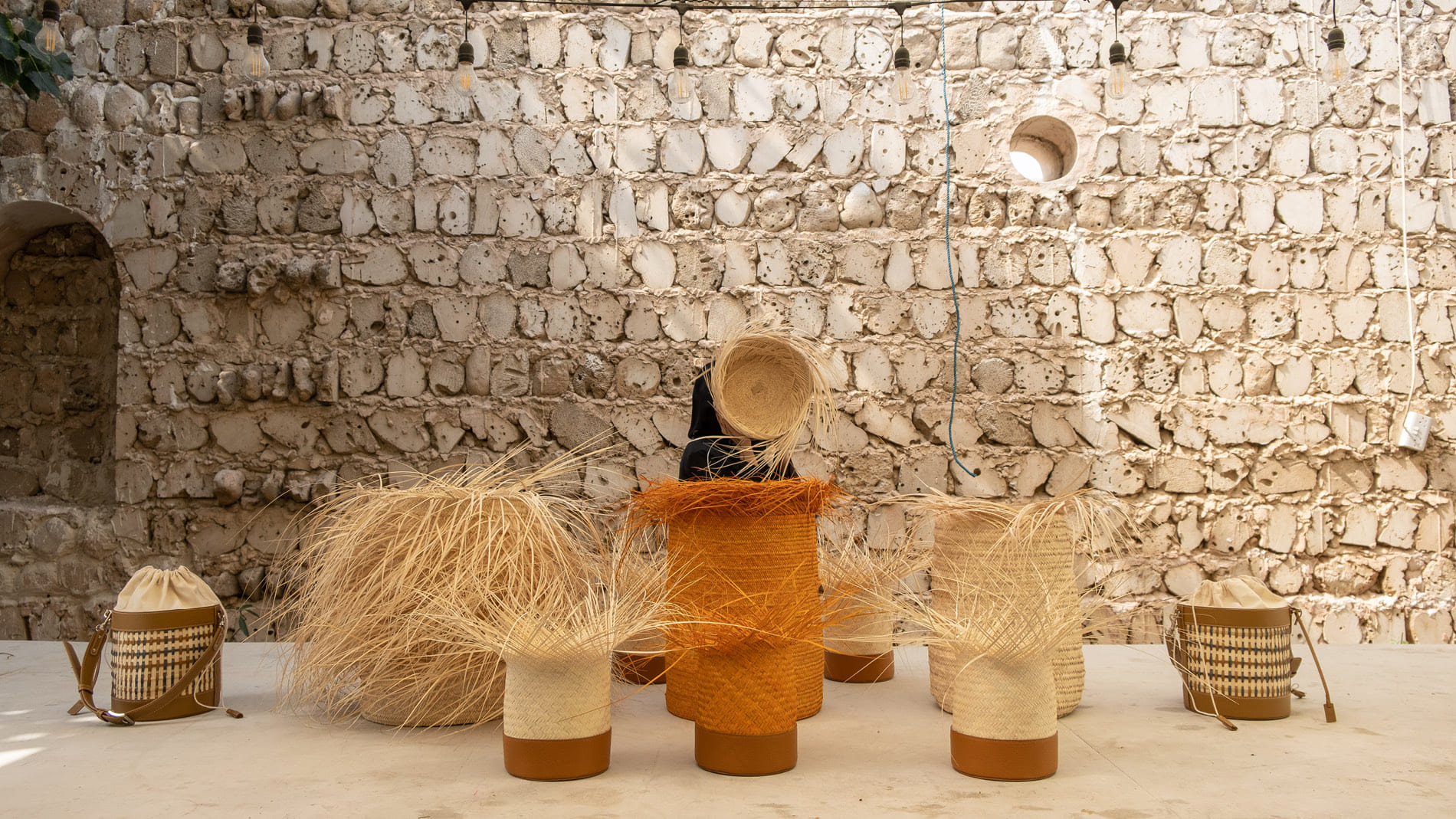
Irthi Contemporary Crafts Council connects female Emirati artisans with international designers, fusing traditional handcrafted woven techniques with modern manufacturing methods and product categories.
Based in Sharjah, the cultural capital of the UAE, the initiative was founded by Her Highness Sheikha Jawaher Bint Mohammed Al Qasimi and offers training programmes, mentorship schemes and access to new market opportunities for its growing members. Irthi is building a database of traditional craft terminology and patterns, documenting each term’s origin and the artisans producing it today. The Thaya Collection is a contemporary interpretation of Safeefah palm frond weaving, also using camel leather, cotton, silk and recycled felt to create homeware items traditionally found in Emirati homes. By preserving this legacy and sharing centuries old knowledge, Irthi is protecting the UAE’s rich craft legacy and sharing it with future generations.
irthi.com
@irthicouncil
Turquoise Mountain
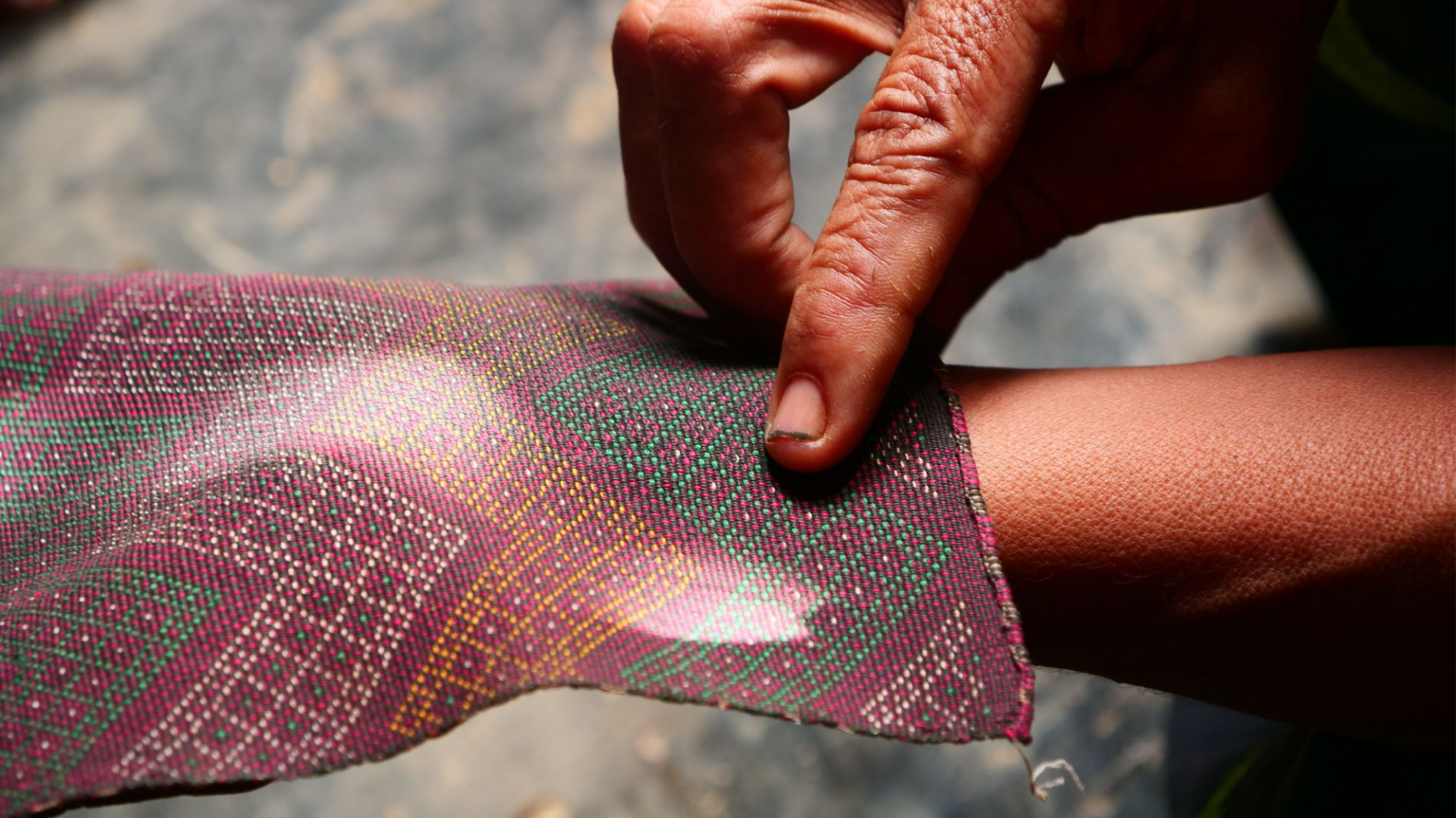
Turquoise Mountain works to preserve historic areas and cultural communities in Afghanistan, Myanmar and The Middle East. Reviving local skills and traditional crafts helps to create jobs and restore a sense of local pride.
Founded by King Charles III and supported by donors and charitable partners, the organisation connects artisan entrepreneurs and small businesses with regional and international commercial opportunities. From weaving to woodwork and jewellery, entry-level and advanced apprenticeship programmes at training centres and in refugee camps are creating a new generation of artisans, while branding, production and financial training drives economic development.
Norlha
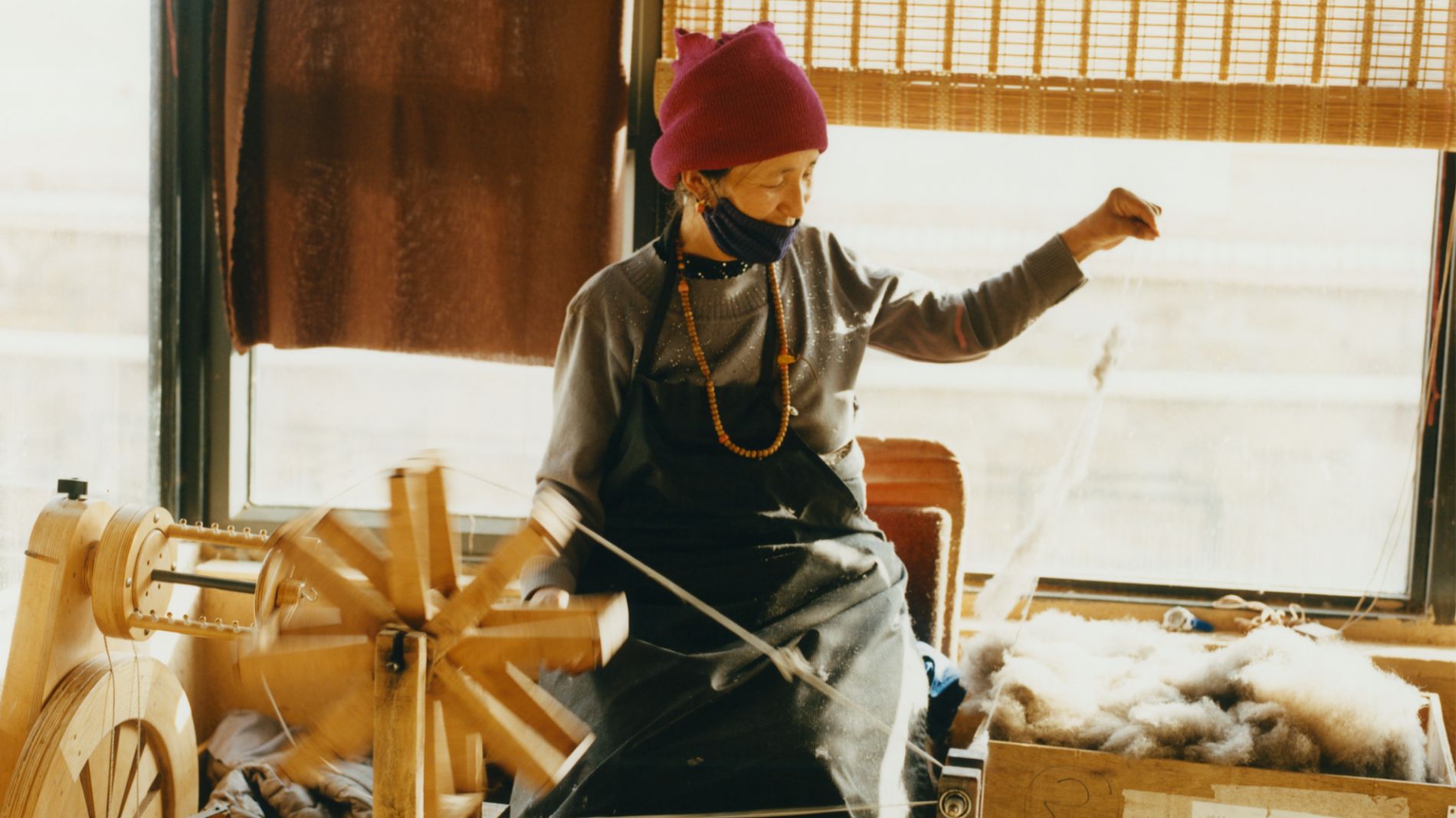
Handcrafted by nomad families on the Tibetan Plateau, Norlha creates premium apparel and homewares from yak khullu wool.
Founded by a mother-daughter duo in 2007, Norlha now employs 130 local craftspeople, some of whom have spun, woven and felted local yak wool for many generations. Balancing modern technology from India and Nepal with traditional Tibetan artisanal knowledge ensures the preservation of skills for the future, as well as providing training and employment opportunities for the local community. In recent years, herders invested in higher numbers of cattle which had a damaging effect on the land. With Norlha now providing an alternative source of income, there is less competition among herders and the cattle can feed from better grassland.
Restoring Biodiversity
How can we revive plant and wildlife ecosystems damaged by modern material supply chains?
Regenerative practices must take a multispecies approach to encouraging biodiversity. Acknowledging the threat of extinction, addressing the causes of loss, and reviving habitats for diverse plants and wildlife aids ecological restoration.
Climafibre
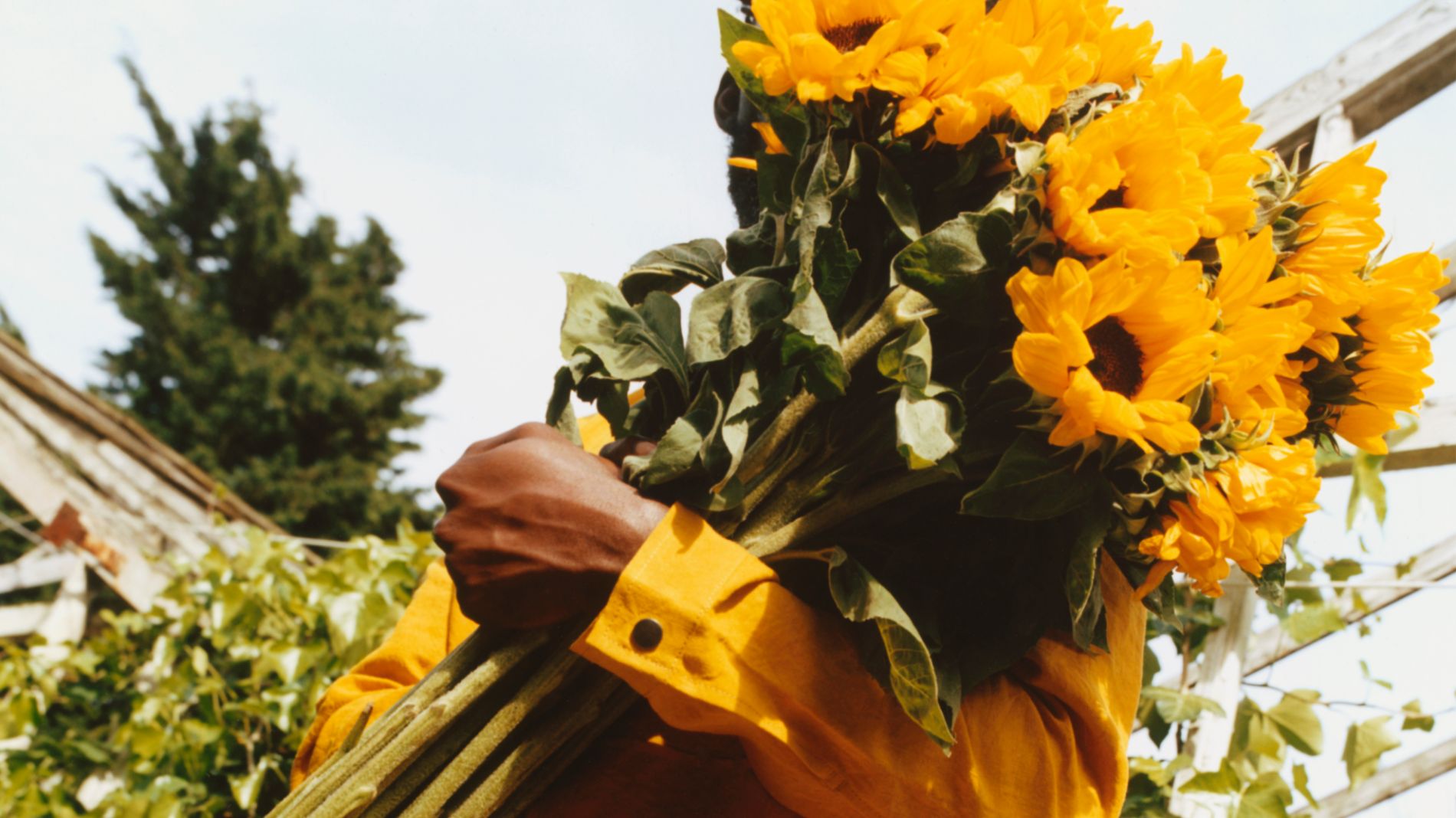
Led by multidisciplinary designer Jess Redgrave, UK-based Climafibre is working on material solutions for the fashion industry that support regenerative farming and food systems using sunflowers.
When companioned and rotated with other food crops, sunflowers help replenish soil and boost biodiversity thanks to their extensive root system. A species that can be grown globally and requires minimal intervention, fertilisers or watering, sunflowers’ resilience offers huge potential for climate change adaptation. Using the whole plant, Climafibre produces fibre for textiles from the stem, natural dyes from the flower and water-resistant coatings from sunflower seed oil industry by-products.
jessredgrave.com
@jess_redgrave
Modular by nature by Omlab
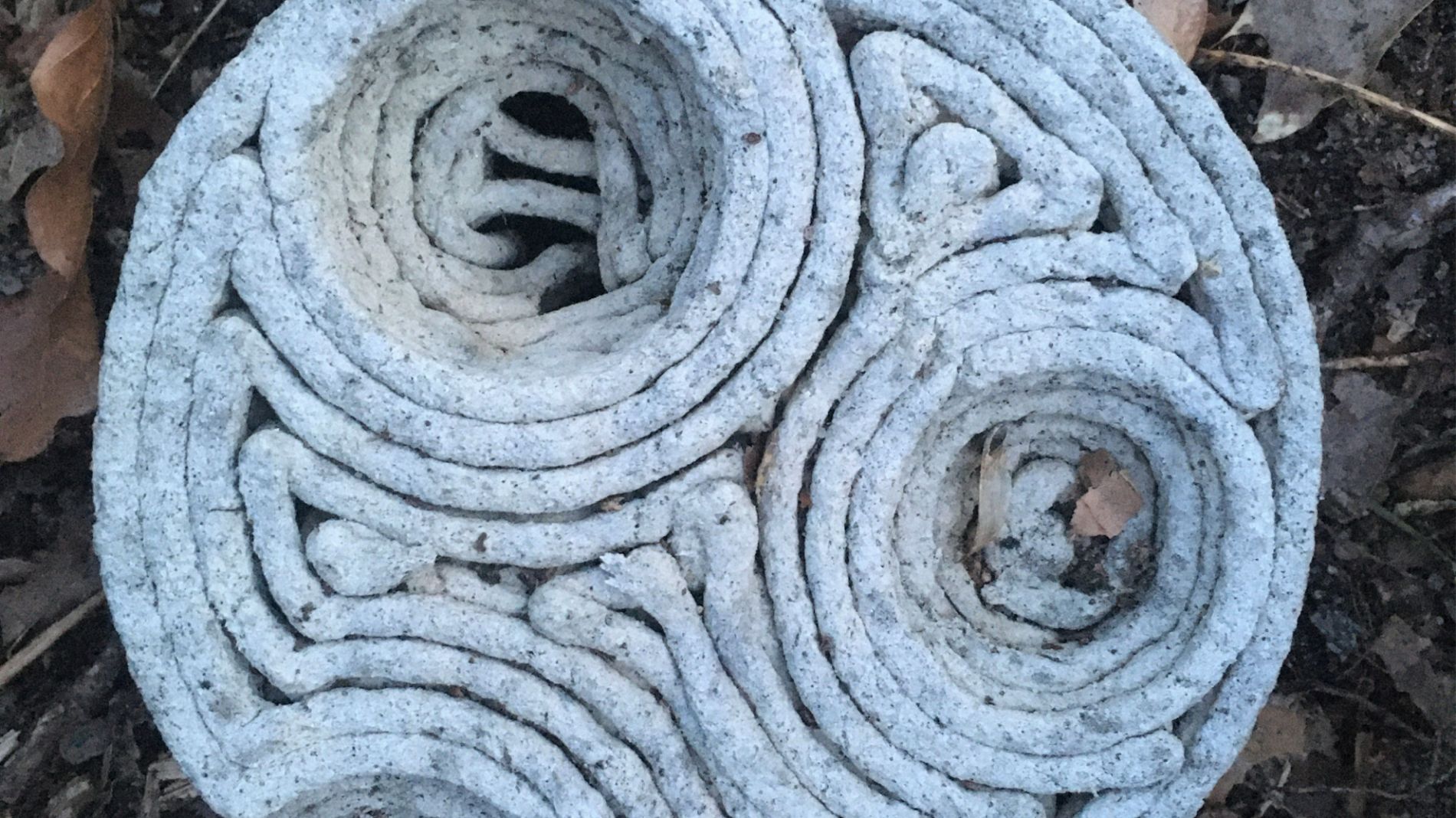
Research-based design studio Omlab creates nature-friendly products for the construction industry using raw materials already in circulation.
Aiming to leave the earth intact, Omlab uses no fossil fuels, minerals or chemicals, developing ecologially-sound, bio-based construction products that respect and give back to nature at end-of-life. Blending tertiary ‘waste’ such as cellulose, alginate and calcite from sewage works, clay-like materials are 3D-printed and dry to a similar strength and appearance to concrete. A collaboration with architecture film MVRDV, Modular by nature saw Omlab’s prototype Itbettermatter used to create insect and bird houses for a vertical city garden. Also biodegrading into calcium-rich matter, the material benefits soil diversity and plant growth.
Flocus
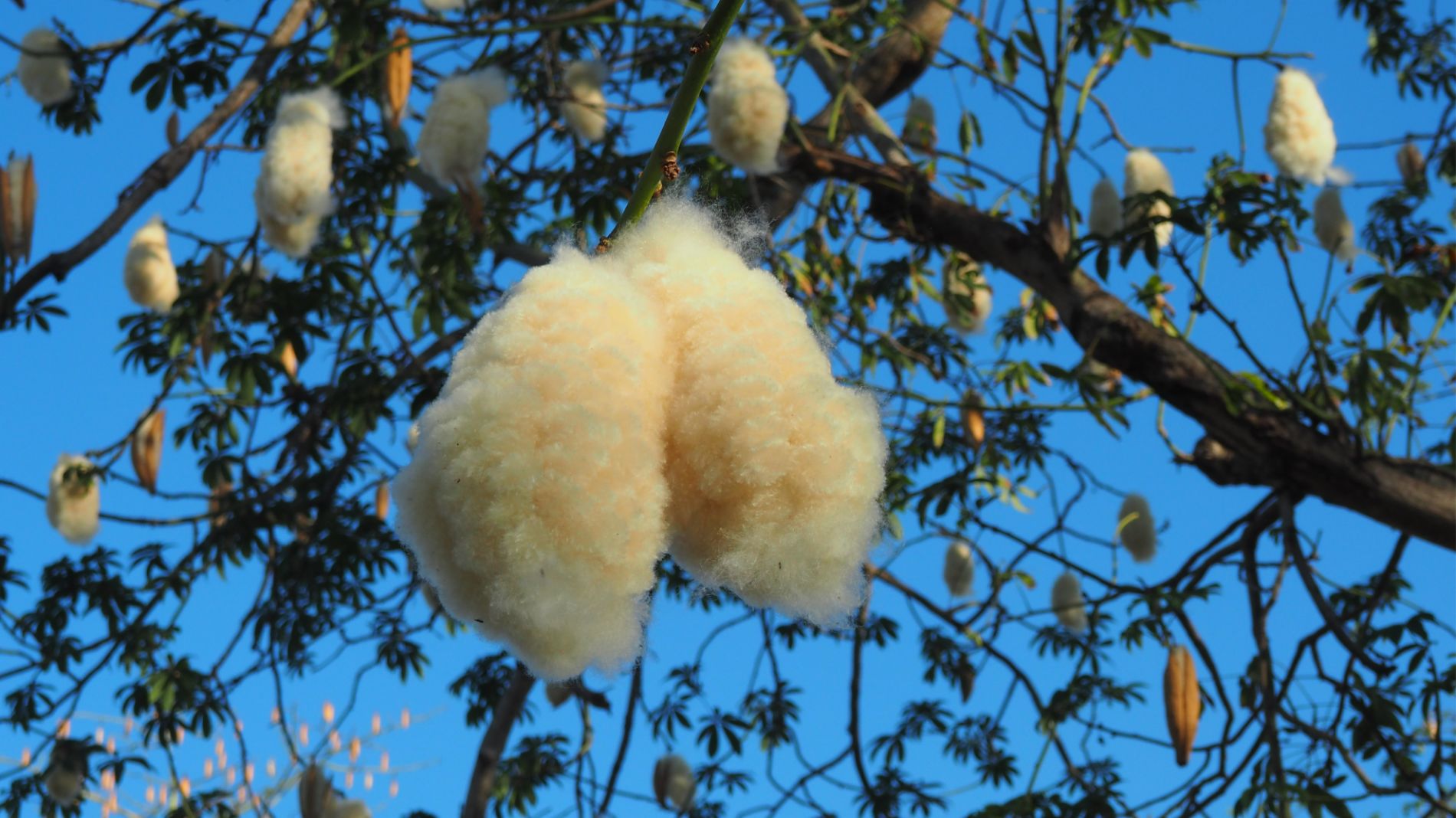
Netherlands-based Flocus is creating a responsible supply chain and new uses for kapok, a regenerative, soft organic fibre traditionally used as a stuffing filler.
Able to thrive with little human intervention on non-agricultural land and as farming companion crops, kapok trees boost local biodiversity, improving soil and air quality by naturally storing carbon. Harvested like fruit, kapok pods require no chemical processing or water consumption, meaning the crop has a positive impact on the communities in which it is grown and sourced. Lightweight, antibacterial, moisture and temperature regulating, Flocus fibre is recyclable and biodegradable, and can be spun into fine yarn or blended with other materials to create more sustainable fashion, interior or industrial textiles.
Biological Fabrication
How can we combine natural materials with high tech synthetic innovation to create alternative material supply chains?
The convergence of science and design offers huge potential for new materials, from living microbial systems to synthesising nature’s regenerative powers. Growing and extracting next-generation materials using innovative, highly-productive processes can create plentiful resources from minimal input.
Radiant Matter
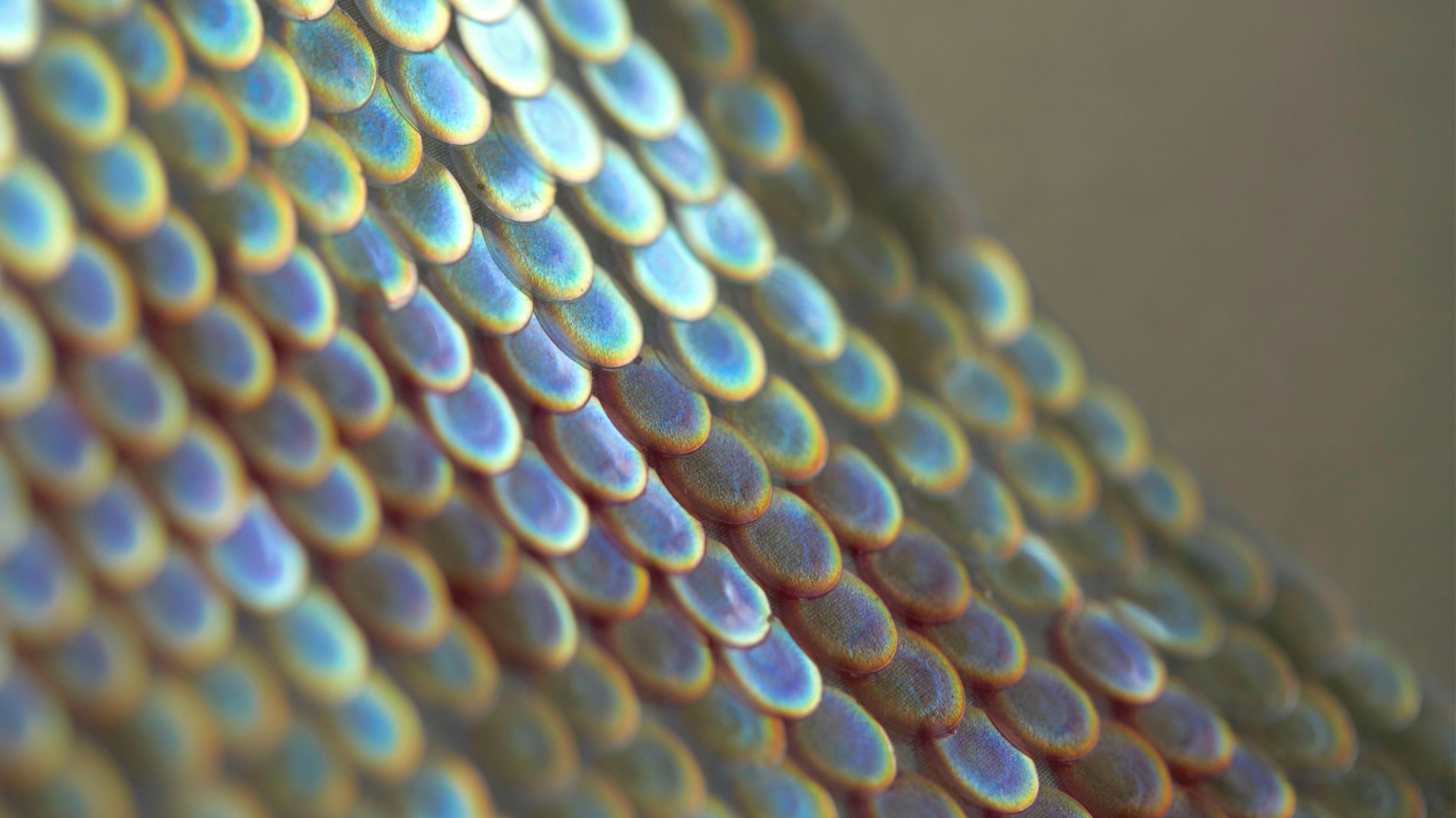
UK-based Radiant Matter is a material science company creating naturally sparkling and vibrantly coloured materials from highly-renewable cellulose, an abundant polymer found in plants, fruit skins or recycled paper.
Conventional sequins are made from small discs of PET or PVC with synthetic, metallised coatings. Considered a toxic microplastic, many leak into our water supplies, while others end up in landfill. Inspired by the natural iridescence of peacock feathers and jewel beetles, Radiant Matter's structurally coloured and shimmering material is created from cellulose. The result is a lightweight, colour-fast, non-toxic, low-carbon and biodegradable material that doesn't require metals, minerals, pigments or petroleum. Radiant Matter's first application, the BioSequin, has captured the excitement of the apparel industry as seen in their partnership with fashion brand Stella McCartney.
Modern Synthesis
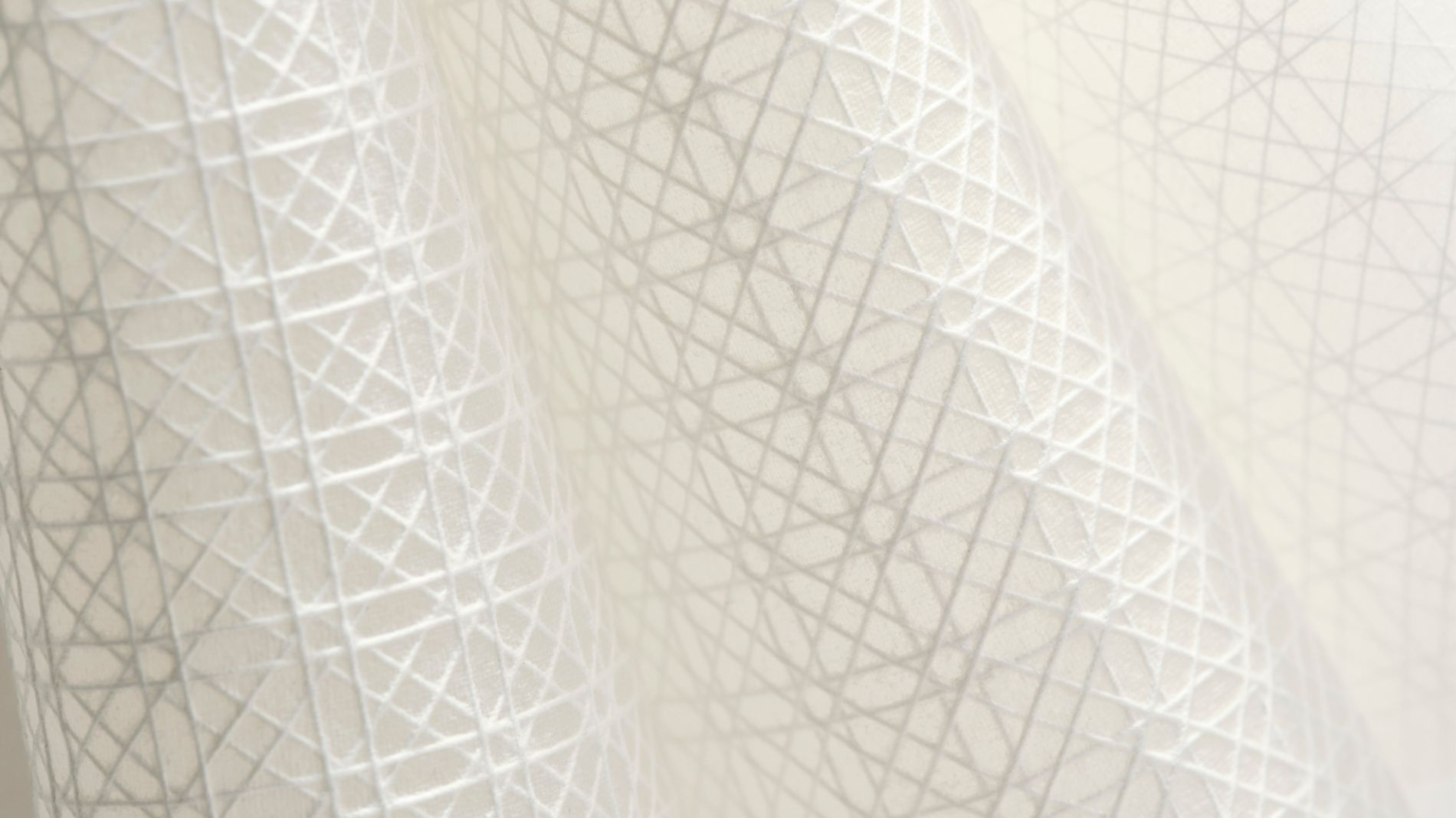
London-based biotech company Modern Synthesis works with bacteria to produce nanocellulose-based biomaterials, a new class of textiles designed to displace leathers and coated synthetic textiles.
Bacteria grow the raw material, nanocellulose, as a natural by-product of fermentation. Modern Synthesis then creates a customised nanocellulose biofilm, which they combine with a natural textile to create a versatile range of non-woven materials. This unique approach to material design allows designers to precisely control the final look, feel and function of the biotextiles, which can be further enhanced with other finishing processes and naturally derived coatings. Offering performance without plastics and aesthetics without animal inputs, these biomaterials can be applied across the fashion industry and beyond.
Charlotte Werth
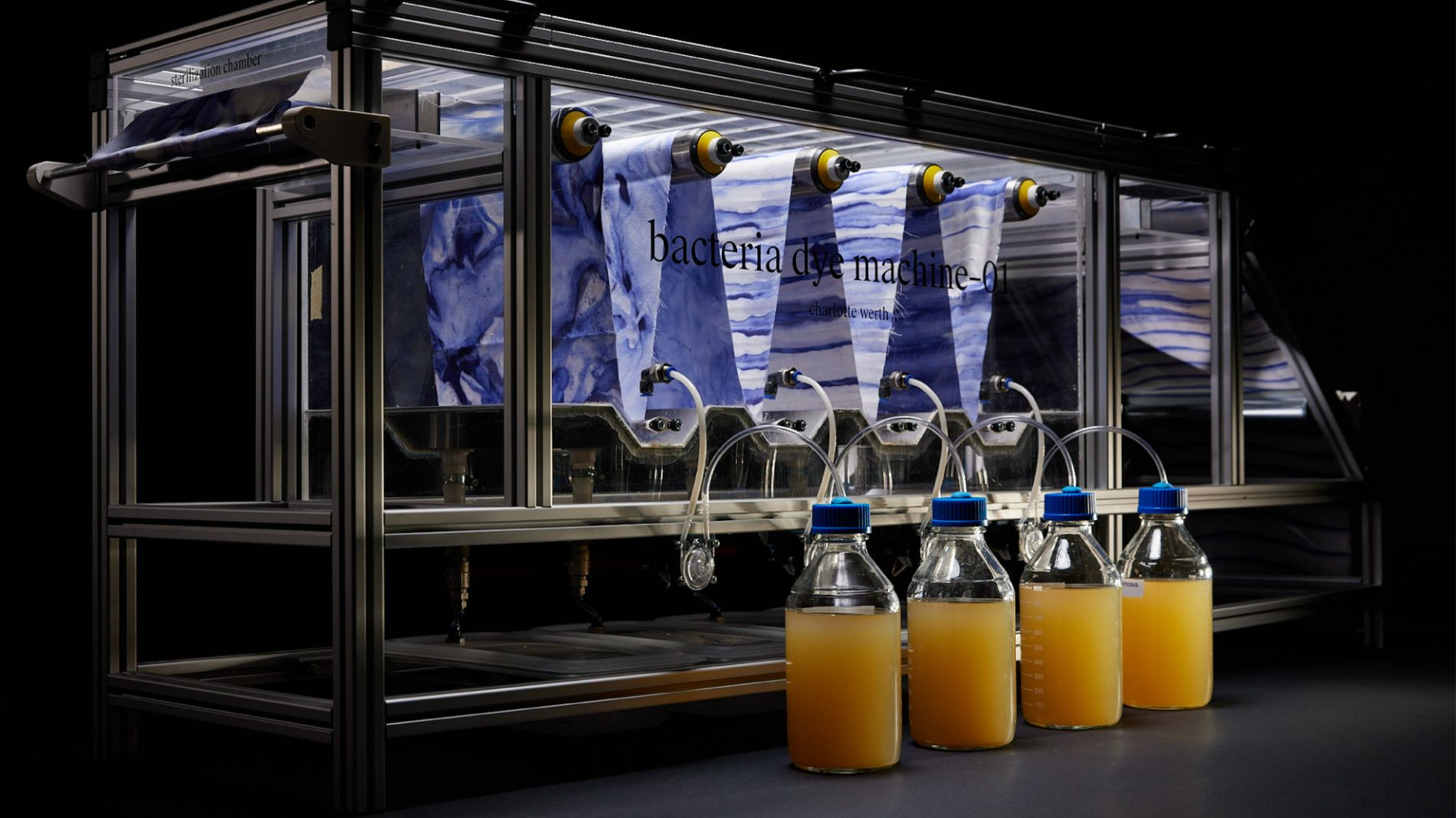
A recent graduate of MA Material Futures at Central Saint Martins, designer Charlotte Werth has developed a printing process that uses bacteria to create pigments.
A bath of yeast extract, salt, protein and glucose provides food for the soil-dwelling bacteria Janthinobacterium lividum, which grows and populates, turning a cloudy yellow colour when ready to produce purple pigment on fabric. Werth’s Bacteria Dye Machine slowly moves fabrics through the bath, stopping to allow pigment deposits, then low-energy UV light sterilises the fabric. Using less water than synthetic dye processes , folding, pleating and multiple dye runs creates different patterns and effects, all printed on luxury deadstock fabric including silk, viscose and wool.
charlottewerth.com
@charlottewerth_
Naturally Abundant
How can we broaden our currently limited palette of materials, considering what is locally and globally abundant?
Highly-productive, resilient raw materials that grow with little human intervention offer naturally high yields, strengthen soils and capture carbon. These abundant, versatile crops could help move the focus away from traditional natural material fibres that require high levels of water, pesticides or fertilisers.
Kelsun™ by Keel Labs
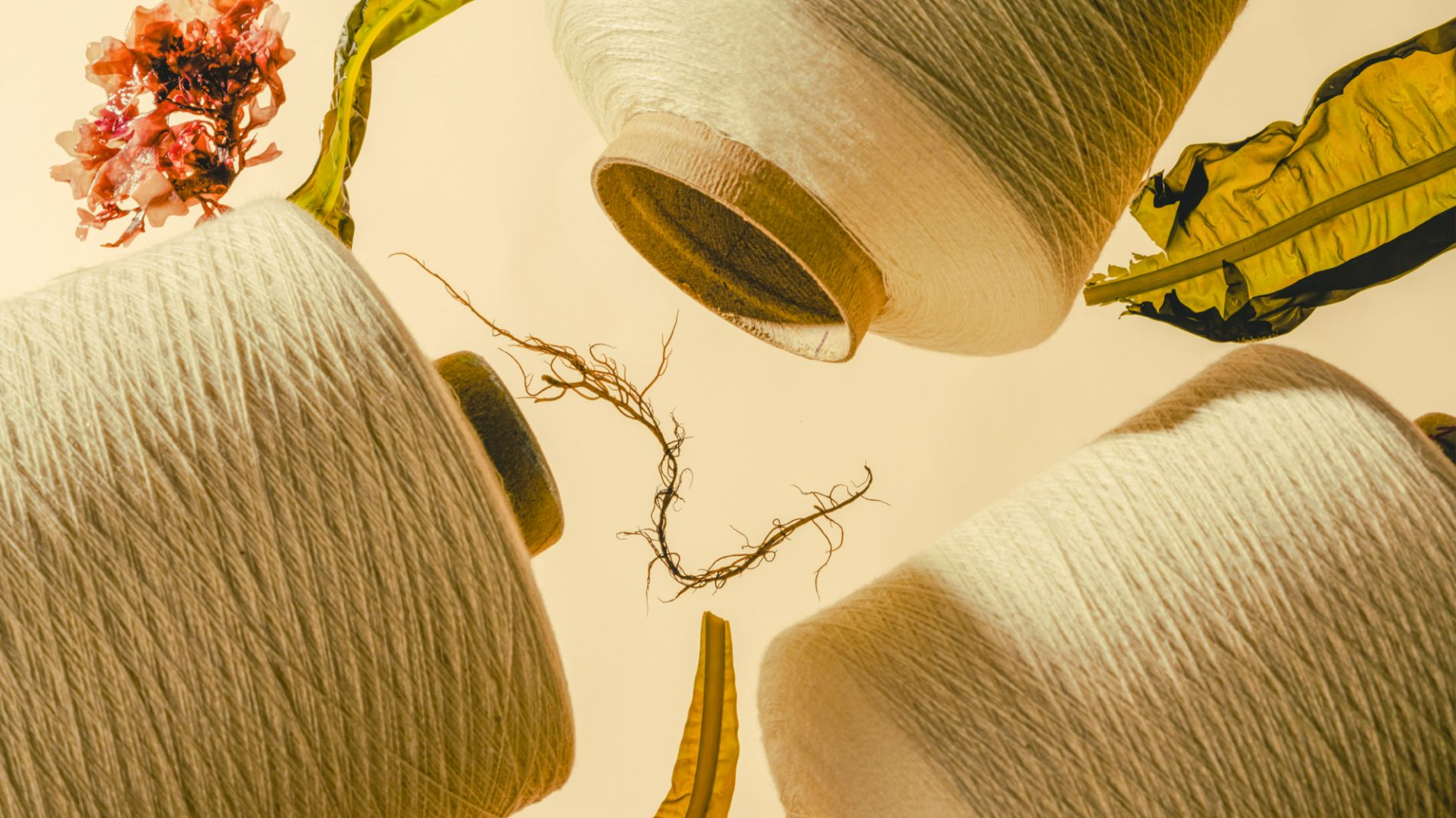
US-based innovation platform Keel Labs is exploring the ocean’s regenerative power and potential as a climate-focused material resource, creating a textile industry yarn made from kelp.
Keel Labs takes inspiration from the efficiency of marine ecosystems, and believes that materials should be regeneratively grown, renewably sourced and created without environmental harm. Its star product Kelsun™ is a seaweed-based yarn created from an abundant polymer found in kelp. A naturally regenerative organism that is easy to grow, kelp absorbs carbon dioxide in the ocean while improving local habitats, and is harvested under strict sustainability guidelines and within local harvesting calendars.
Margent Farm
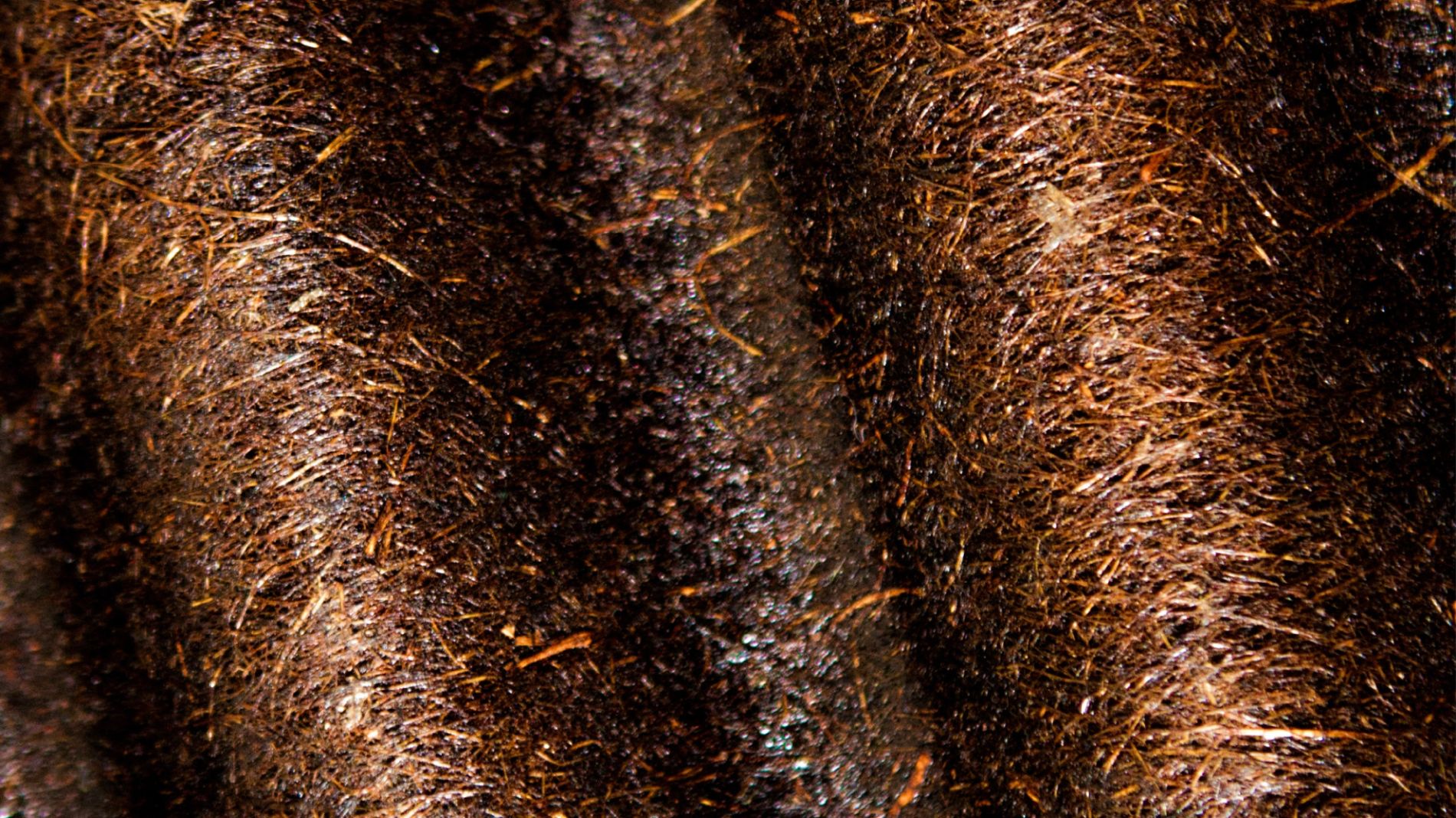
Margent produces hemp on a 50 acre regenerative farm in Cambridgeshire, UK, creating a range of materials for use in the construction, fashion and beauty industries.
A fast-growing and low maintenance crop, hemp’s deep roots work to regenerate soil and purify the air, capturing and storing carbon. Once a popular farming crop in the UK, hemp became rare after strict laws were imposed due to its links with cannabis. Despite this, Margent Farm started life in 2016, building its farmhouse using hempcrete from its first harvest. It now produces a range of materials from hemp fibre, such as corrugated wall cladding sheets and hemp and PLA placemats.
Mogu
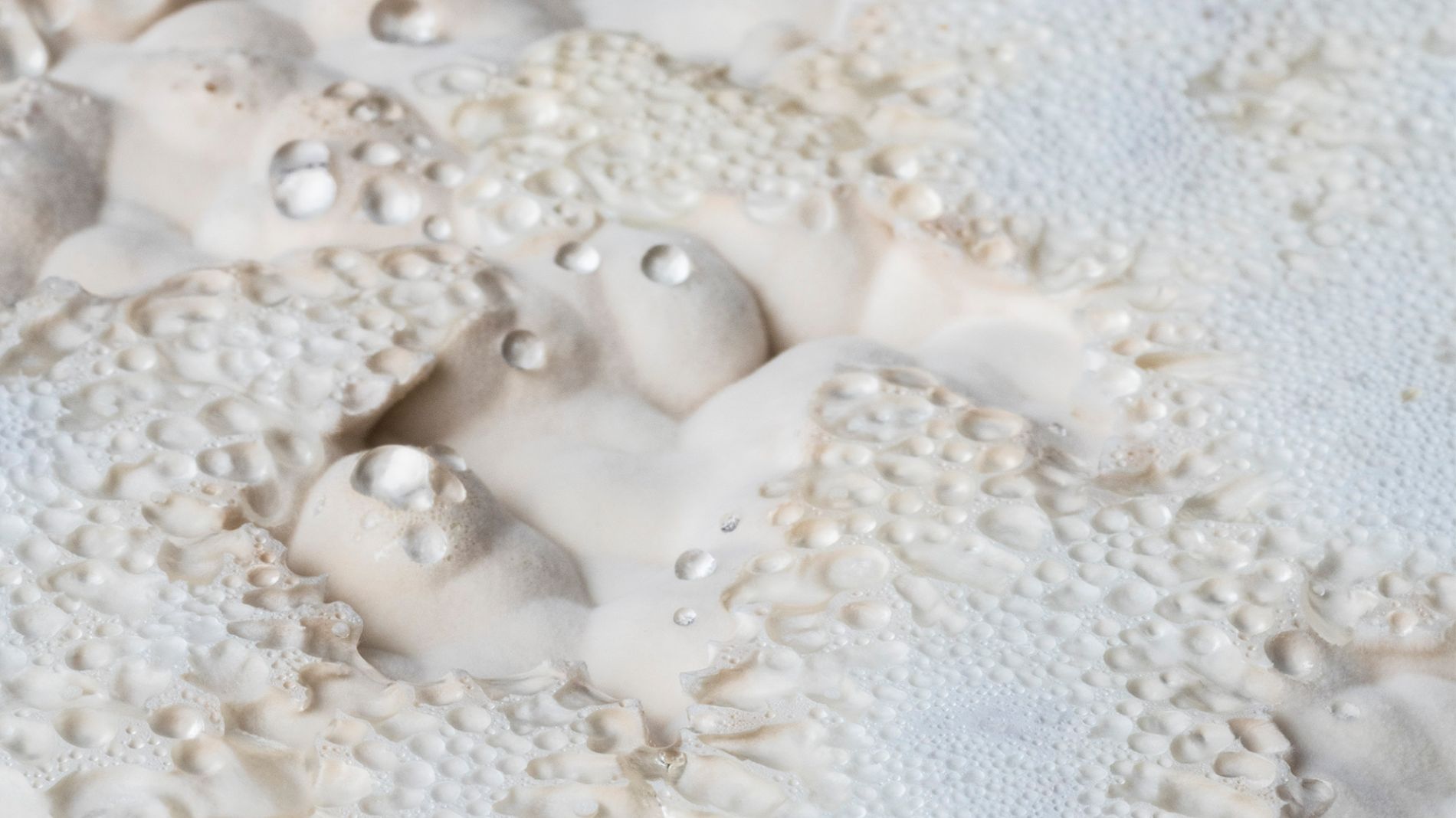
Italy-based Mogu believes in the power of nature to radically disrupt the design of everyday products, with a portfolio of high-end, low-impact, mycelium-based interior materials.
Mogu’s circular process uses low-value, agro-industrial material waste as a starting point, prioritising regeneration over depletion. By applying technology and engineering to grow specific fungal strains of mycelium, they transform the original product into one of higher value in a short time frame without impacting people or the planet. Creating beautiful, functional and biodegradable products in a range of 3D shapes and colours, Mogu’s acoustic panels are soft and foam-like, their decorative wall coverings are slim and sound-absorbing, while their bio-based flooring tiles offer durability and modular solutions.
Reclaiming Material
How can we tap into existing agricultural and industrial waste streams to create new materials?
Extracting raw materials, making products, then discarding them and their by-products is contributing to the global waste problem. By putting useful waste streams back into production we can better utilise existing resources and avoid the notion of waste altogether.
Malai
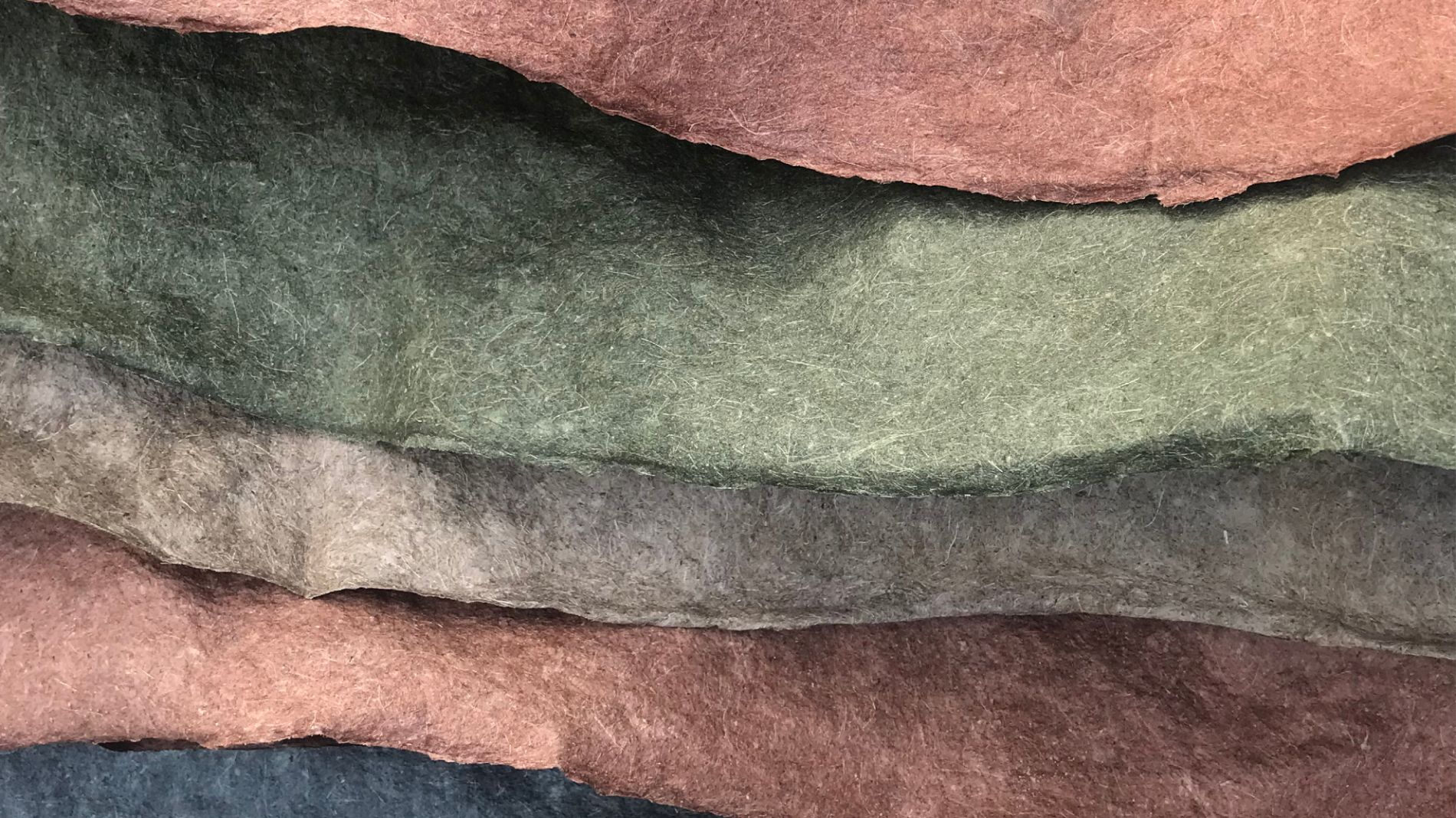
Working with Southern India’s coconut farmers, Kerala-based Malai creates vegan and compostable coconut leather materials for the fashion industry from waste coconut water.
A new material developed from organic bacterial cellulose, Malai is grown on agricultural waste from the coconut industry. Rescuing coconut water destined for dumping or drainage systems after the coconut flesh has been harvested, the water is stored, sterilised and used to feed bacterial cultures, eventually producing sheets of flexible, durable, leather-like material with water-resistant properties. An entirely natural biocomposite material with aesthetic appeal, the material can be moulded into seamless 3-D objects and is available in a range of 10 naturally-dyed shades.
Studio Sarmite
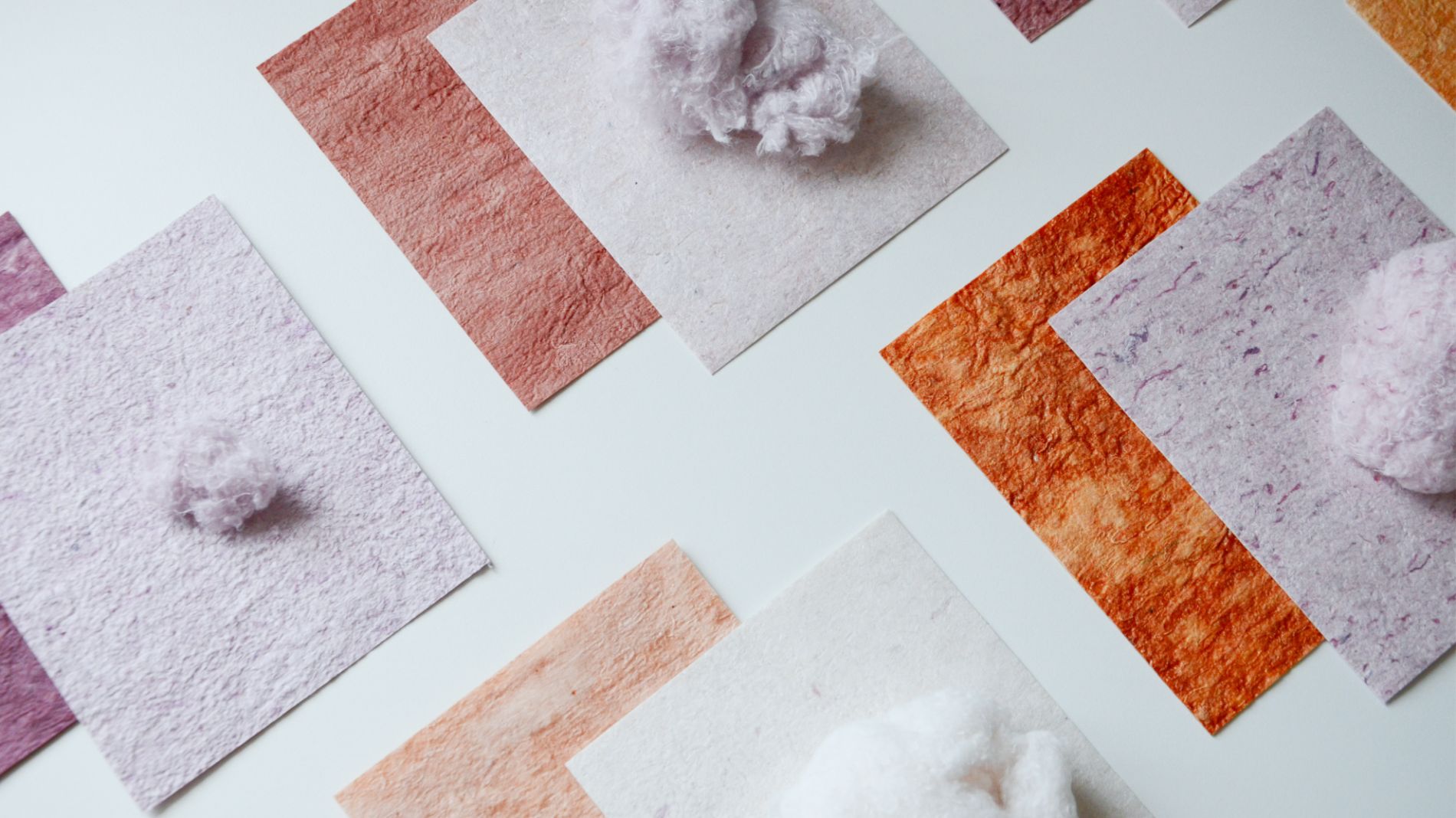
Frankfurt-based Studio Sarmite is a materials and research studio that transforms organic and synthetic industry waste and by-products into high-quality new materials.
Led by designer Sarmite Polakova, the studio believes that waste should be seen as surplus, as all resources can be used to create something new. (UN)WOVEN is a recycled biotextile made with mixed blend, previously unrecyclable fibres destined for landfill. The leather-like material can be dyed with natural pigments extracted during the recycling process to create pleasing colours and playful patterns the purple samples were made in collaboration with natural dye expert Roua Alhalabi of Amsterdam-based Roua Atelier. And at the end of its life, the material can be dissolved in water and the textile fibres repurposed for a new production cycle.
DESSO by Tarkett
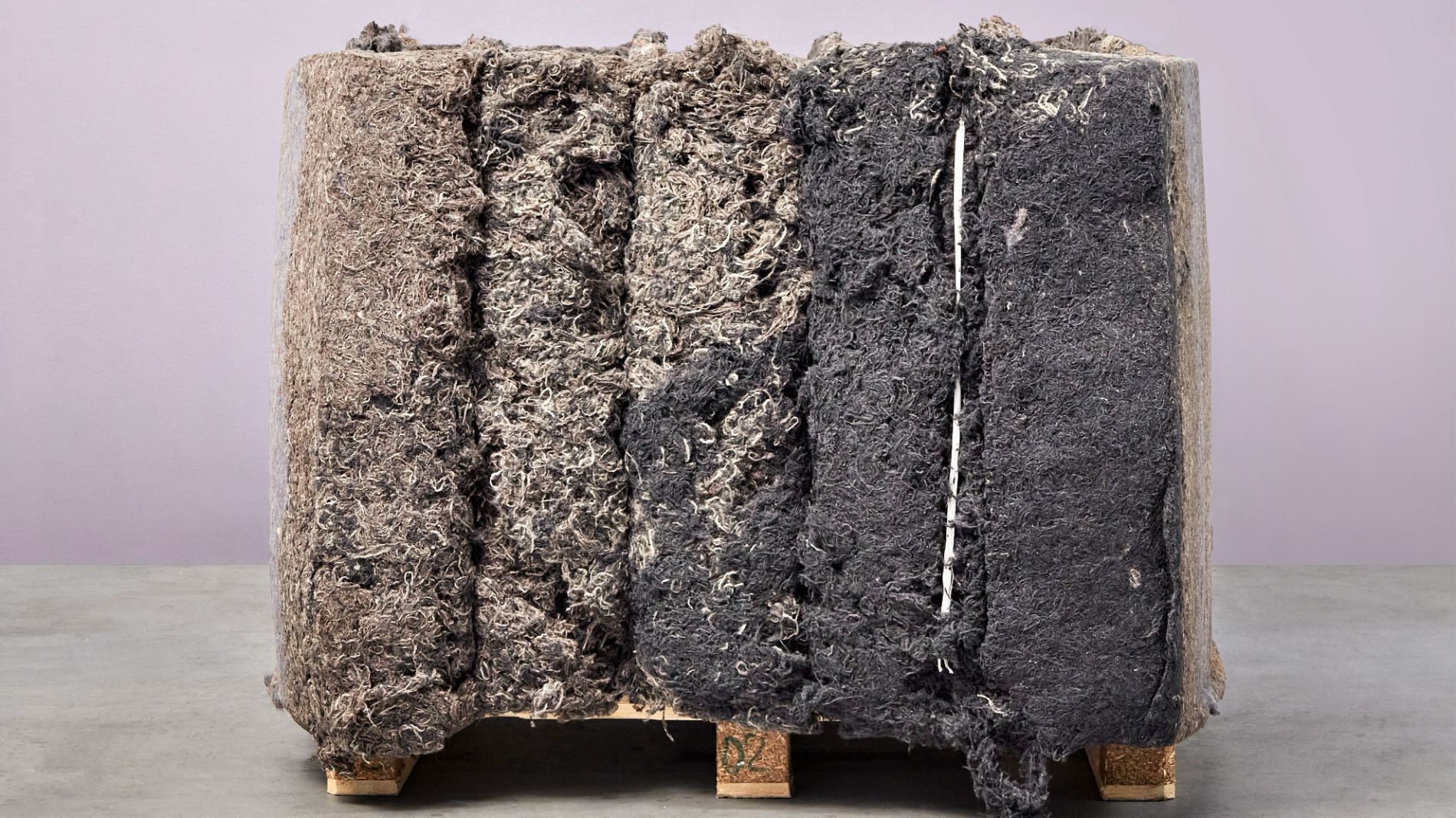
A global flooring company with world-leading technical expertise in closed-loop systems, Tarkett creates materials with multiple lives in mind.
Through their carpet tiles, Desso by Tarkett builds circularity into the start of the design process. EcoBase® backing and pile can be taken apart at the end of their long working lifetime, returning to the production cycle at Tarkett’s own carpet recycling centre, alongside repurposed industrial waste such as chalk from the local drinking water industry. Post-consumer yarn is reworked into ECONYL® by recycling partner Aquafil, and Tarkett’s ReStart® scheme welcomes all carpet back at the end of each life, repurposing and guiding it on to its next role. The company’s latest launch AirMaster uses complex weave tech to capture dust particles to improve indoor air quality.
The Beauty of Circularity: Designing truly circular carpet tiles | Tarkett
@tarkettofficial
@desso_carpets
Radical Transparency
How can we create traceable global material supply chains that tell the full story of material life cycles?
By using science and technology to create tools and processes that capture and record data along supply chains we can understand the social and environmental impact of the materials we consume. Encrypting materials helps brands track their footprints and life cycles, and communicate this information to customers in a meaningful, trustworthy and accessible way.
Haelixa
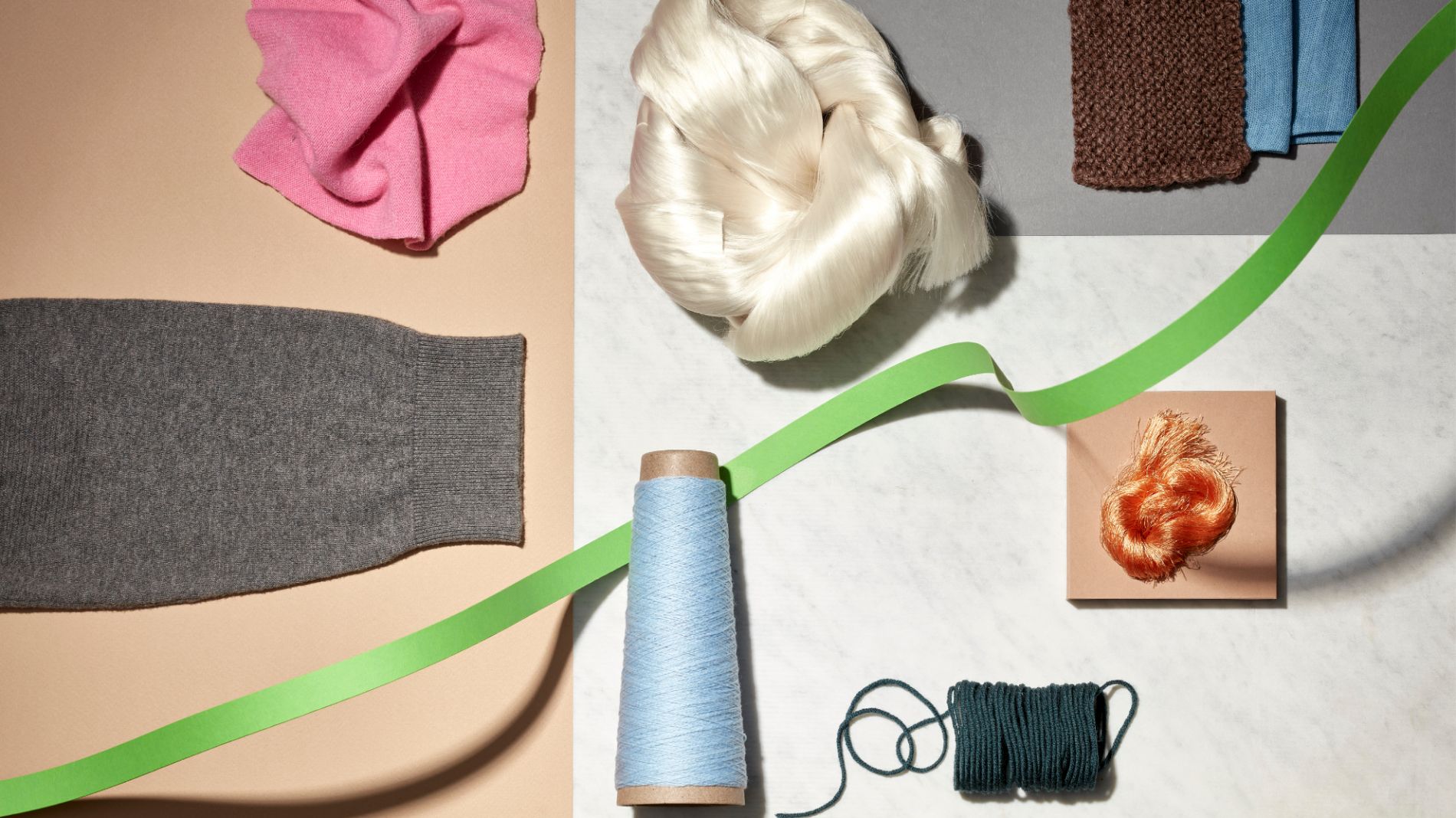
Founded by doctors with a background in chemistry, Swiss-based Haelixa is revolutionising the traceability and transparency of material supply chains by physically applying DNA to raw materials.
Haelixa’s technology marks, traces and authenticates products along the supply chain. The company creates a distinct DNA code for each supplier, brand, collection or material, and applies it with a customised spraying system that can withstand production steps and will not harm the product, environment or humans. The information can be verified by forensic PCR technology to support product claims such as origin, process, recycling and authenticity, and can be applied to textiles, gemstones and precious metals.
FibreTrace®
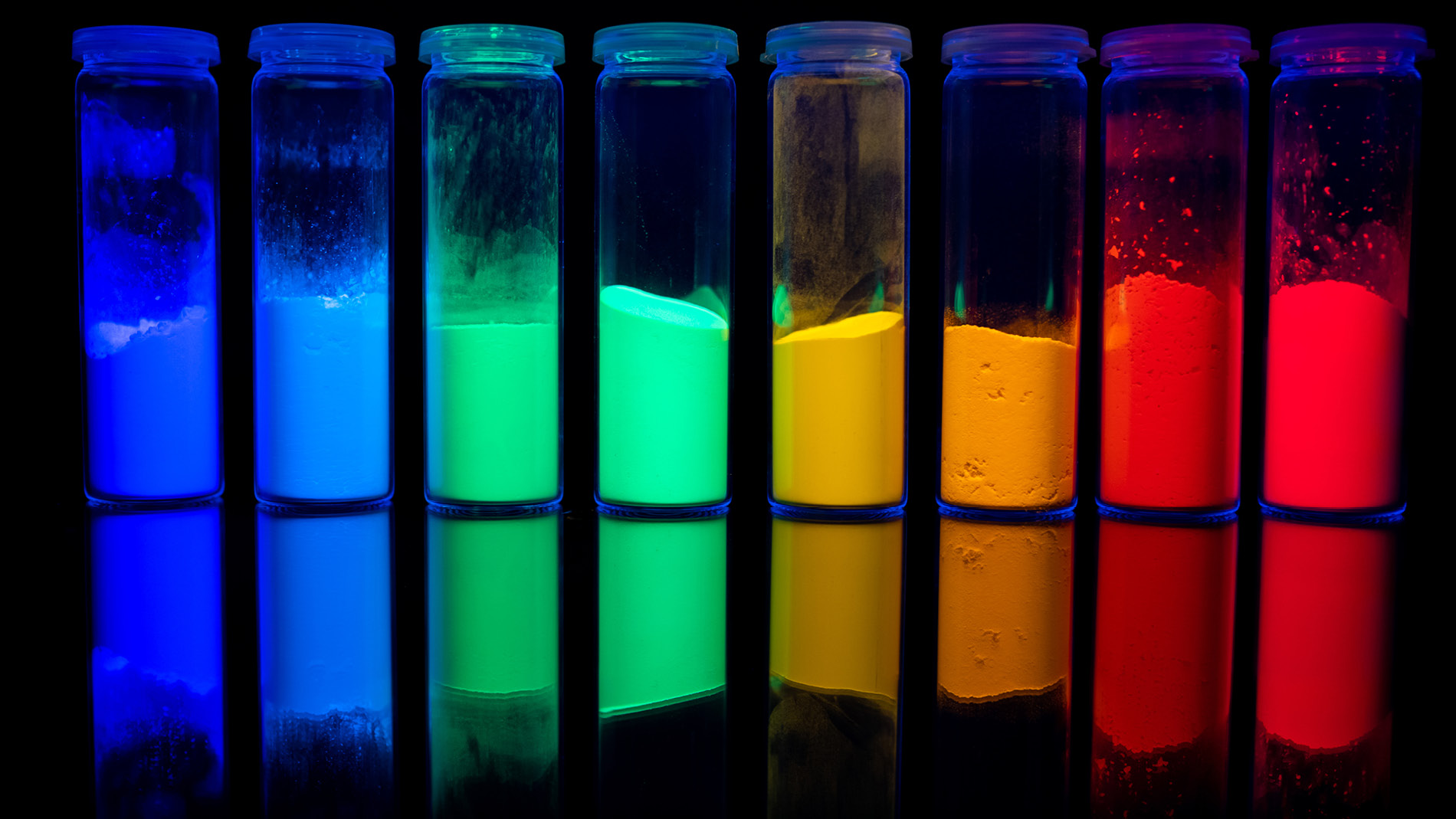
FibreTrace® connects digital traceability with physical technology to track and verify fibres throughout the global supply chain, from raw material to retail store, to reuse and recycling.
With a focus on transparency, honesty and accountability, FibreTrace® Verified embeds patented luminescent pigment markers within raw fibres, which are then tracked and verified with unique scanning devices in real-time, and recorded as a digital twin. Each product created in the FibreTrace® system generates a unique QR code which can be utilised on final products and scanned by the customer, sharing details of the product’s journey and all the suppliers involved in its production. By providing advanced traceability solutions, FibreTrace® aims to empower all members of the supply chain with the ability to take direct accountability to reduce the environmental impact of the global textile industry.
Avery Dennison
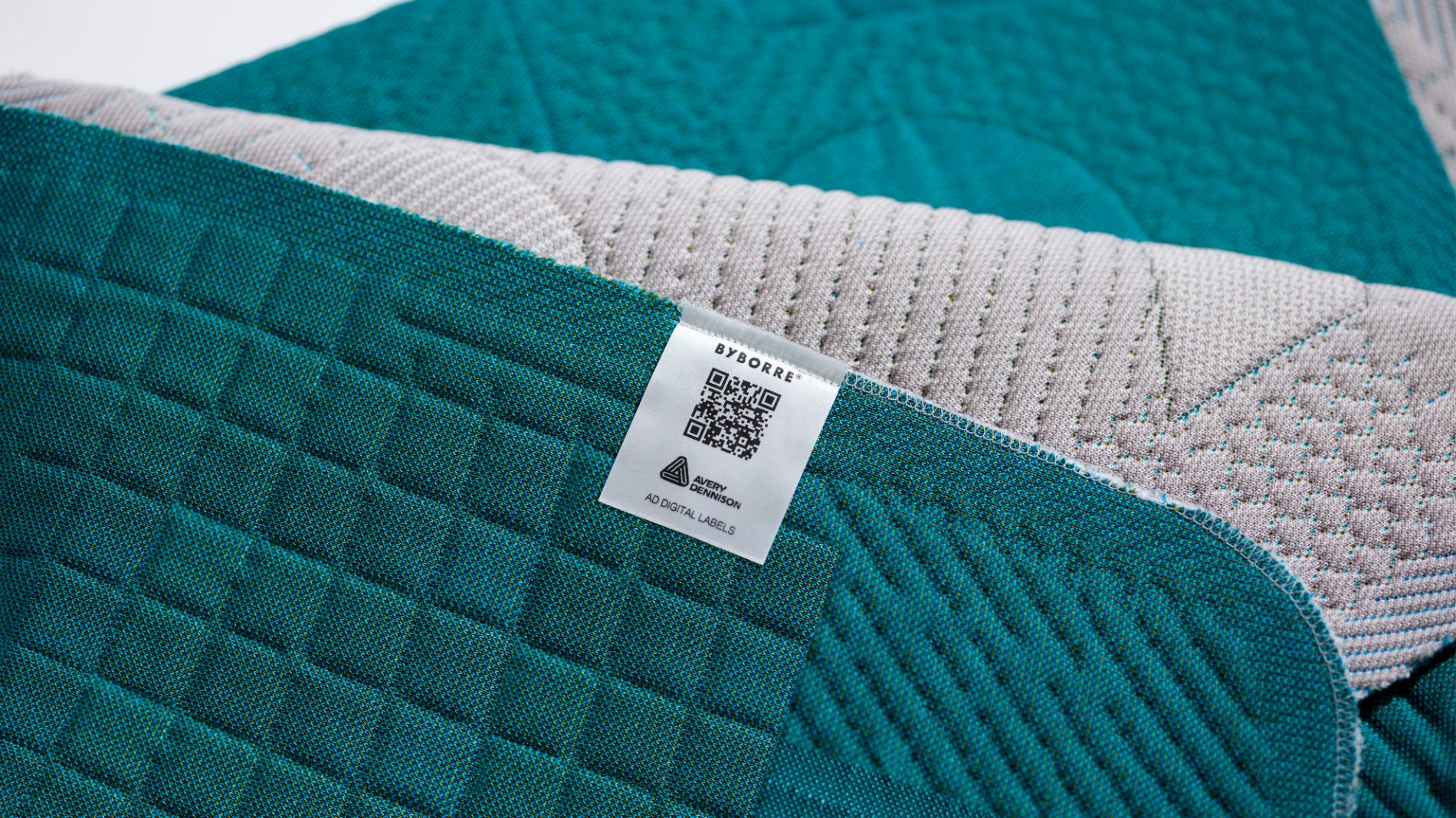
Global materials science company Avery Dennison’s smart labelling solutions help brands facilitate and communicate a more transparent and traceable approach to materials.
Teaming up with a range of fashion and textiles companies including BYBORRE®, Mara Hoffman and Swijin, Avery Dennison’s Digital Care Labels offer access to branded digital experiences. The labels are embedded with unique scannable QR codes powered by atma.io, a connected product cloud, that enable consumers to discover a wealth of information via their smartphones. These details include the product’s complete supply chain journey, its material composition and care instructions, and information on how to repair, recycle and repurpose the item to keep it in circularity for as long as possible.
Cultivating Localism
How can local materials which are harvested and processed in localised areas have a positive impact on people and planet?
By supporting the local sourcing, production and consumption of materials, we can avoid globalised transportation and reduce carbon footprints. Focusing on availability, seasonality and resourcefulness means embracing non-standardisation, and often improving local environments as well as extracting from them.
Selected works with straw by Material Cultures
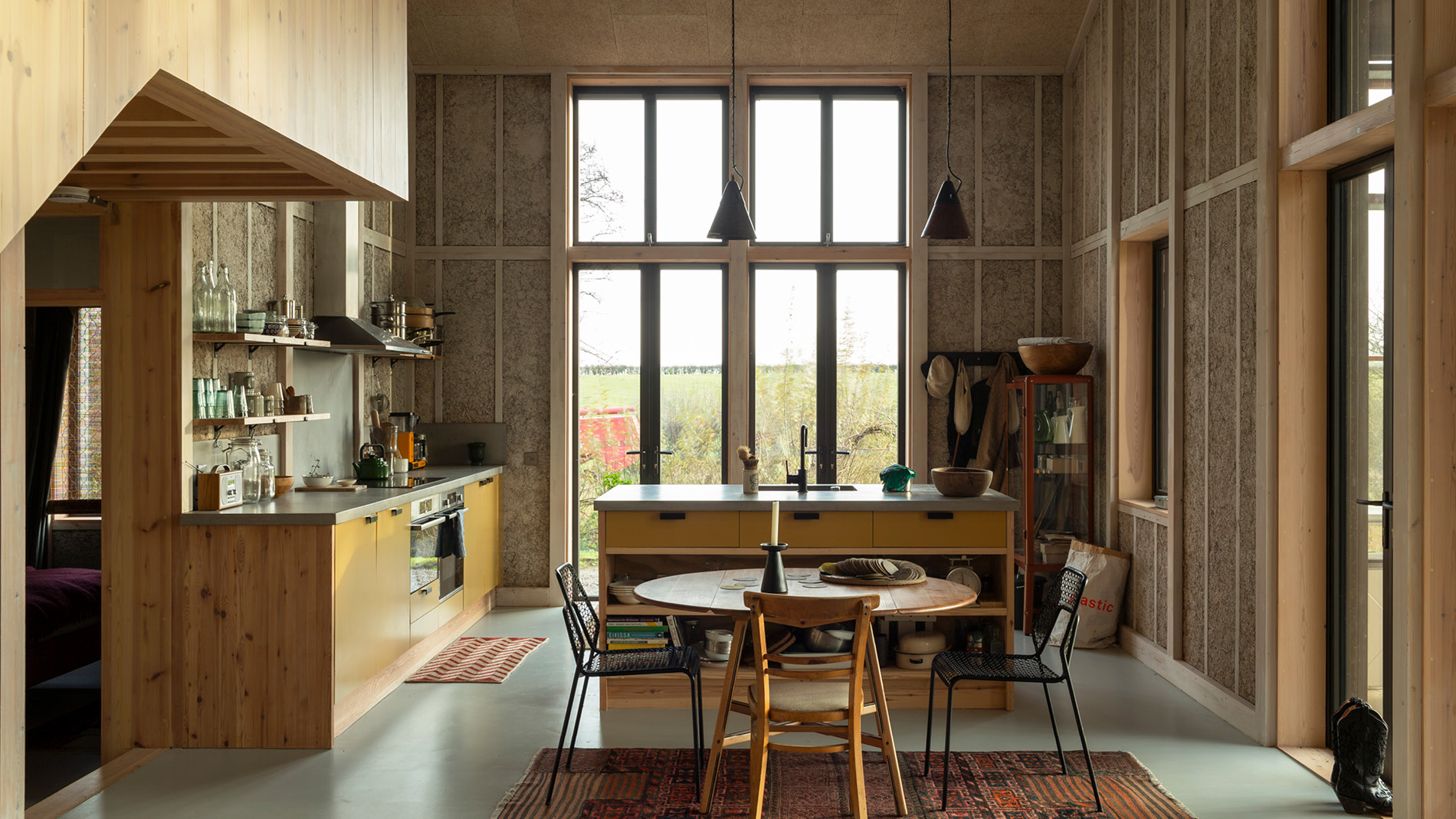
Material Cultures is a UK-based design and research studio that provides design services, undertakes hands-on construction and refurbishment projects, and works with public, private and third sector organisations interested in developing and delivering a regenerative, low-carbon built environment .
These selected works with straw showcase examples of affordable, achievable and low-tech solutions for long-term carbon sequestration and storage. Around 40% of the dry weight of both hemp and cereal straws is sequestered atmospheric carbon. With seven million tonnes of wheat straw produced annually in the UK alone, replacing mainstream, petrochemical-based construction technologies with plant-based systems could turn the buildings themselves into a globally significant carbon sink, alongside the oceans, soil and forests.
Studio Sanne Visser
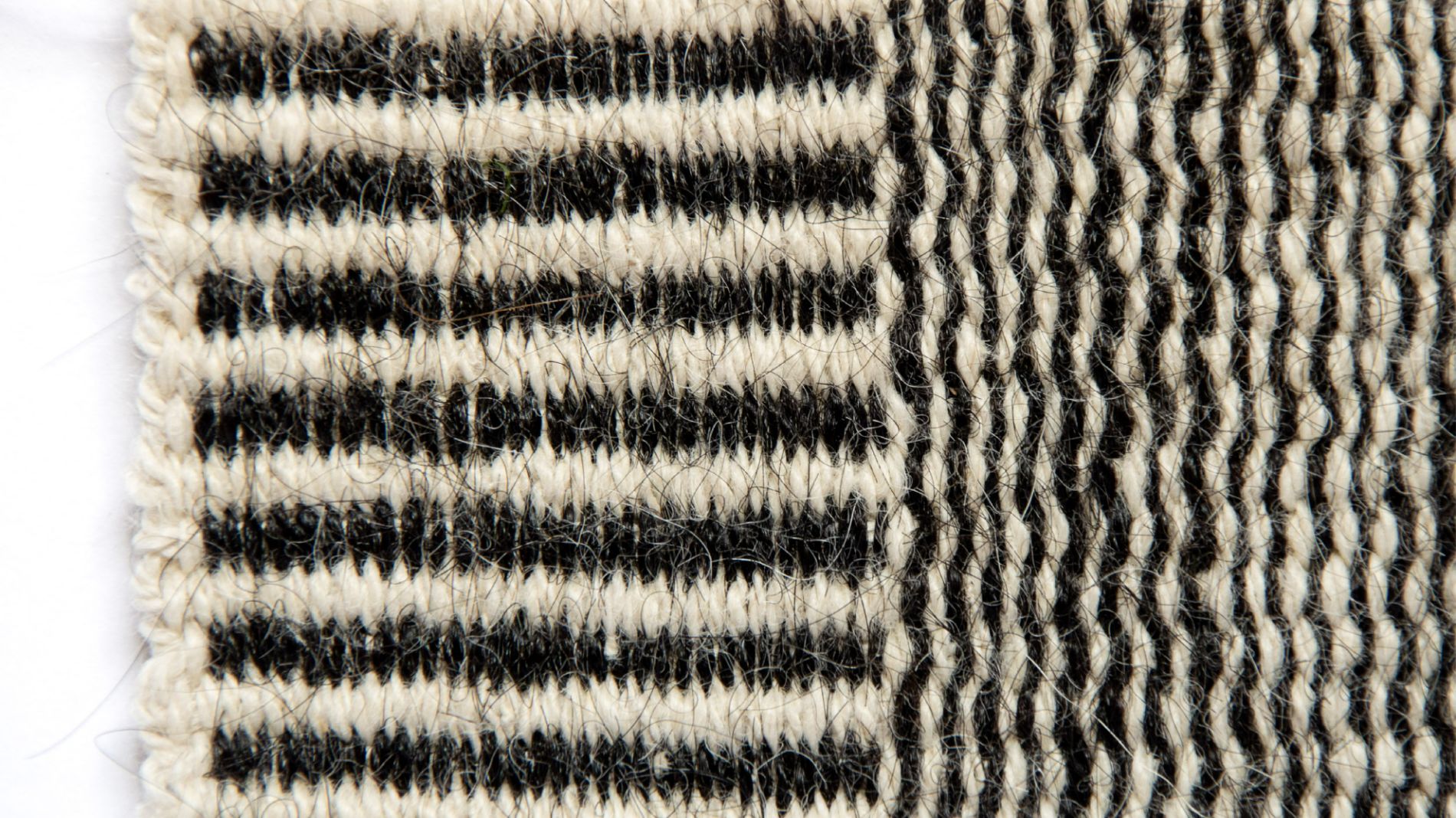
Dutch designer Sanne Visser is a material explorer, maker and researcher focusing on material innovation, sustainability and future thinking.
As Design Researcher in Residence at London’s Design Museum in 2022, Visser began to explore human hair as a local waste stream and recycled material resource in a project called Locally Grown. Collaborating with a community of hairdressers and barbershops, she redesigned a barber’s chair to catch hair as it is cut, as well as a sorting system to categorise hair on locality and needs. Creating hair wool and handspun yarn using traditional rope making techniques, hair fibres can be made into woven textiles, interior products and even dog leads, to be sold locally within the communities where the hair is sourced.
Atelier NL
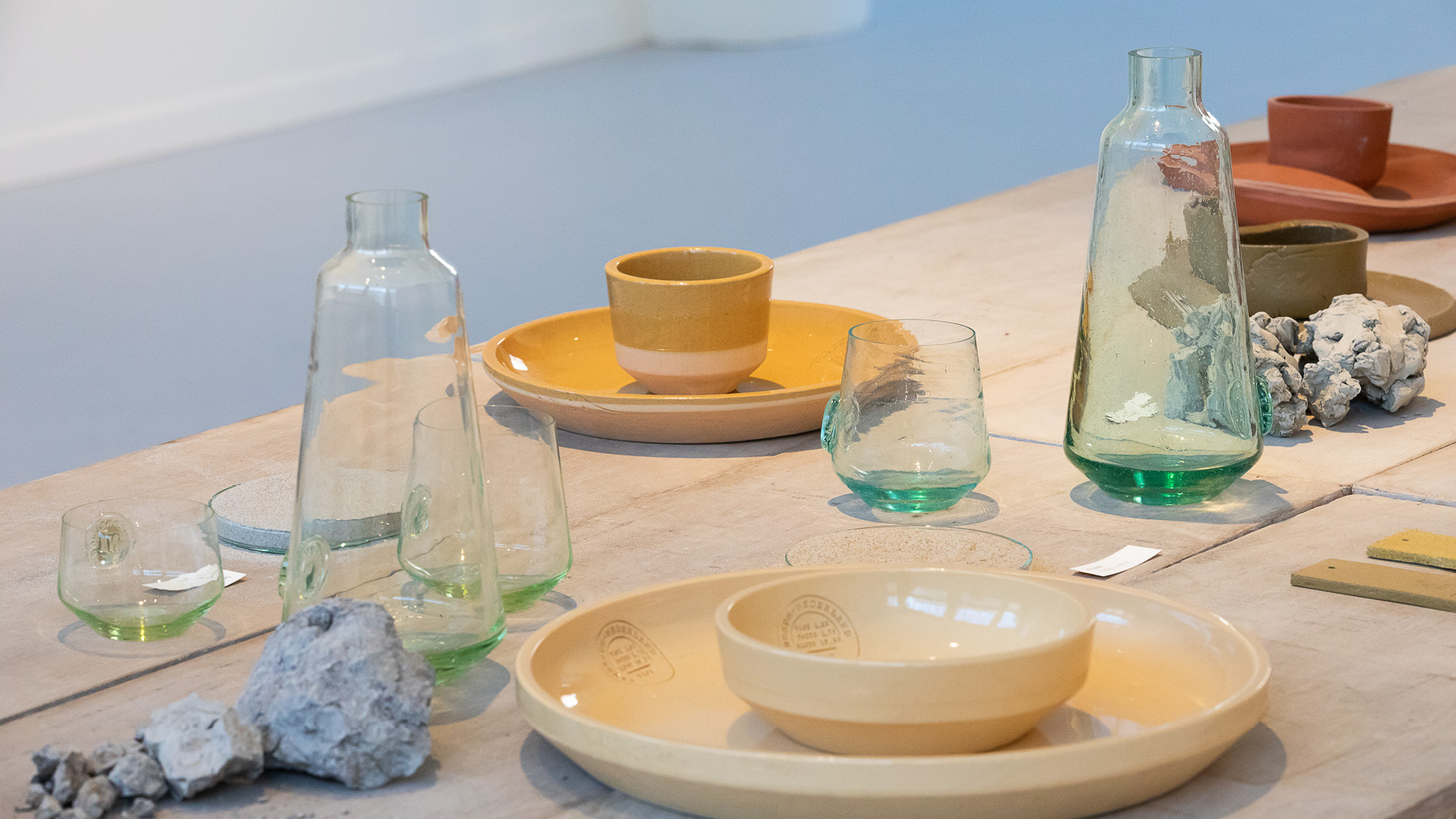
A design studio celebrating the value of local materials, Atelier NL reshapes raw earth elements into everyday objects, reflecting the subtle variations of the natural world.
Co-founded by Nadine Sterk and Lonny van Ryswyck, the Eindhoven-based studio honours cultural heritage and inspires appreciation for the planet’s resources, using locally-sourced wild sands for glassmaking and clay for ceramics. Atelier NL’s Clay Service is a handmade dinner set of plates, bowls and cups created from clays collected across Europe, each chosen for their geological, historical and social significance. Varying considerably in colour depending on the chemical components of the local soils, each piece carries a stamp that links it directly to its place of origin.